Precisely fitting metal processing
7 tips for successful metal bending
Do you need bent metal for a project? Below we explain the most important types of metal bending and answer further questions!
1.500+
Satisfied customers
5.500+
Available machines
0,11%
Complaint rate
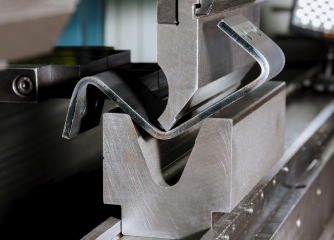
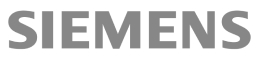
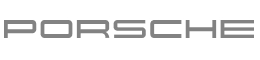
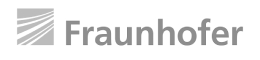
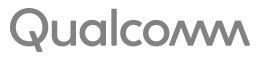
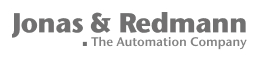
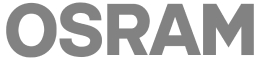
Metal bending made easy
The following tips can help you with your first small projects in particular. It is also always advisable to carry out a test bend on a test piece before you start working on the intended metal sheet.
7 tips for successful metal bending
Minimum bending radius as a valuable parameter
The minimum bending radius is the smallest possible radius that you must achieve in order to successfully avoid cracks in the bending zone. It should therefore always be calculated precisely. It is determined, among other things, by the alloy material and the thickness of the sheet metal you have. In the case of steel, experience has shown that it is around one to three times the sheet thickness.
You can use this calculation as a rough guide:
- Steel = sheet thickness x 1
- Copper = sheet thickness x 1.5
- Aluminum = sheet thickness x 2
Always bend at right angles to the rolling direction
Another tip to avoid breaking the metal piece is to never bend the sheet towards the visible fibers. Instead, bend the metal sheet at right angles to the rolling direction. This reduces the minimum radius.
Simple trick for calculating the bending edge
Would you like to calculate a bending edge that is close to the edge and protrudes a little? No problem. In this case, bend the sheet metal with a longer overhang than you actually need. Then shorten the part that is not needed, which is called the flange, to the actual length.
Consider equalization value
When measuring your metal sheet, bear in mind that the sides will probably shorten due to the bending process. The thicker the metal sheet, the greater the difference can be. For this reason, you should always measure generously and leave a little more material on the blank. The corresponding compensation value depends on the bending radius and can be calculated online.
Table edge for right angle
To create a right angle provisionally, use a table edge. Would you like to create a different shape but don’t have an angled edge of this size? Then simply build a negative form out of wood. It usually works really well.
Sharpening the edge
Once you have bent the metal sheet evenly over the edge, press the second wooden board onto the sheet from the front. A rubber mallet is useful for sharpening the edge.
Protective gloves
Even professionals tend to forget the most important thing in the heat of the project: protective gloves! They are important because the edges of a metal sheet can be very sharp.
Expert know-how
Metal forming
In the metalworking industry, metal bending is one of the most economical forming processes for the production of three-dimensional workpieces.
Would you like to tackle a metal forming project?
Then know-how is required! In the following, we explain the most important types of metal bending in more detail. We also give you tips for successful implementation.
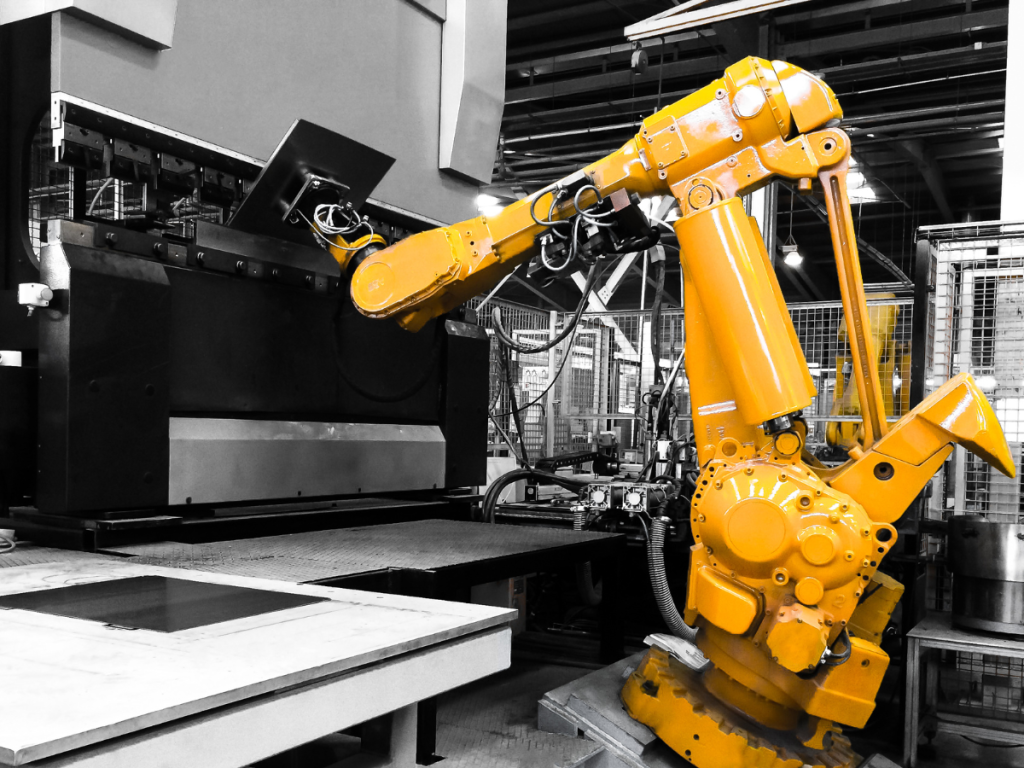
Bending and edging
Can you bend metal?
Yes, but this is not arbitrary. In the case of metal, we speak of forming, bending or folding rather than bending. In most cases, metal is permanently bent into sheet form. Sheet metal is thin and can therefore be easily formed into the desired shape. If the angle is more than 180 degrees, the process is referred to as folding.
Theoretically, very thin types of metal can also be bent by hand. However, this is only recommended to a limited extent, as this process does not always go well – the piece of metal can tear, for example. Professional metal bending with the support of appropriate machines is therefore the recommended method.
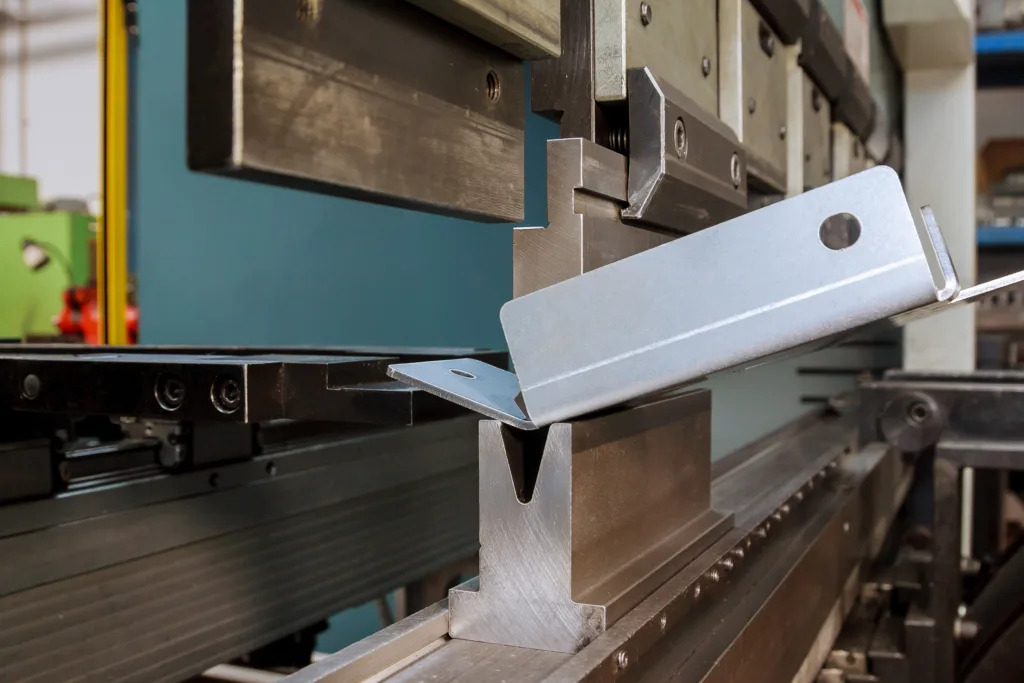
Offer for your components
We will send you a suitable offer for your components within 48 hours
Optimization of your supplier search
Download Whitepaper
Find out now which 9 points you should consider so that you can find the right supplier and reduce your costs by up to 40%.
Please note that the whitepaper is only available in the German language.

The decisive factors in forming are:
The type of metal or alloy
The shape of the workpiece (sheet metal or profile)
The size of the metal piece in cross-section
The type of forming (hot or cold)
The surface structure of the metal piece
The yield strength (elasticity of the workpiece)
Bending and edging at CNC24:
Bending
Technical data
Material thickness: | up to 20 mm |
Available lengths: | X-axis up to 3,100 mm Y-axis up to 2,600 mm |
Ideal batch size: | from 1 – 50,000 pieces |
Our materials
Available materials
Aluminum | Plastics |
Bronze | Copper |
Stainless steel | Brass |
Steel | Titanium |
Inconel | More on request |
Upload
File formats
Get a quote for your parts
We will send you a suitable offer within 48 hours
Metal forming
What methods are there for bending metal?
Various folding and bending processes are used in industrial processing to shape metal into the desired form. Let’s take a closer look at some of these forming methods:
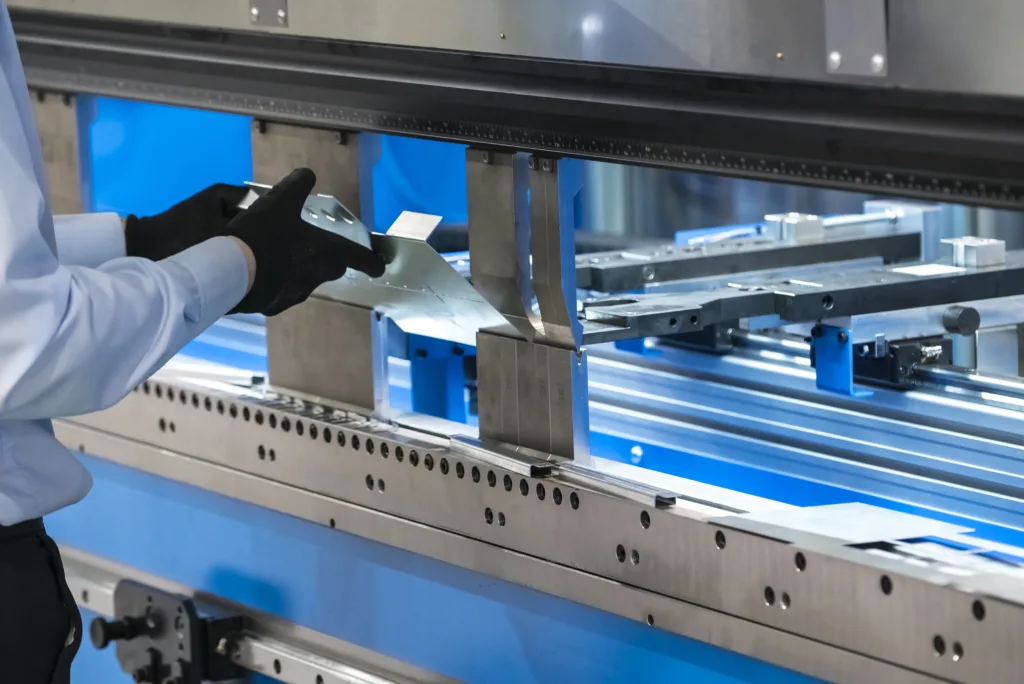
Metal forming by die bending (free bending, folding)
This type of bending of the metal sheet is achieved by using a pre-formed die. The workpiece is pressed into the die by a punch. The space that is created between the punch and the die is deliberately calculated in this way. The punch then moves up again, creating the desired deformation. Fortunately, the machine does not have to be changed for different angles.
The highlight of this process is that the acute angle can be selected individually. The deeper the metal plate is pressed down, the more acute it becomes. The word die is omnipresent in die bending. Dies are preformed parts whose outer shape and outer diameter are exactly the same as the desired inner radius of the bend. Dies are calculated by machine and are also used in the manufacture of pipes in particular.
Bending metals by embossed bending
The metal piece is also pressed into the die by the punch pressure during coining bending. In this case, however, the process is form-fit, which means that the punch is pressed down completely. There is then no free space between the punch and die.
With this pressing process, the die and punch always fit together exactly, which is why the embossing bend produces a very precise result. However, a separate set of tools is required for each desired angle or shape, which makes the processing extensive.
Bending metals by three-point bending
During the three-point bending process, the sheet metal is pressed down onto the die by the punch. This creates the U-opening, in which the workpiece touches the die at three points, which explains the name of the process. This also determines the opening angle, the bottom of the die holds against it.
When bending metal using the three-point bending technique, a precise result can be achieved. Some machines also have an adjustable or mobile counter-holder, which is variable in height. This allows different angles to be implemented without having to change the machines in between. However, precise adjustment can be complex, especially for non-professionals.
Bending metals using the swivel bending process
During bending forming by swivel bending, the sheet metal is fixed in a stop system between the upper and lower beam. The upper beam presses the piece of metal against the pre-formed lower beam. The desired angle is then created by the bending beam by pressing.
The swivel bending machine can create profiles similar to those used for die bending or folding. The difference lies in the process movement, which is straightforward in the case of folding, whereas in swivel bending the shaping is carried out by a rotating tool movement.
Professional reshaping
How are sheet metal tubes and profiles bent?
Bending metal pipes or metal profiles requires a professional. Here again, different methods and equipment are used. The most common are
- Bending presses
- Bending springs
- Hand bending presses
In principle, they all work in a similar way. In all of them, the bending moment is transferred directly to the workpiece and the metal is thus successfully formed.
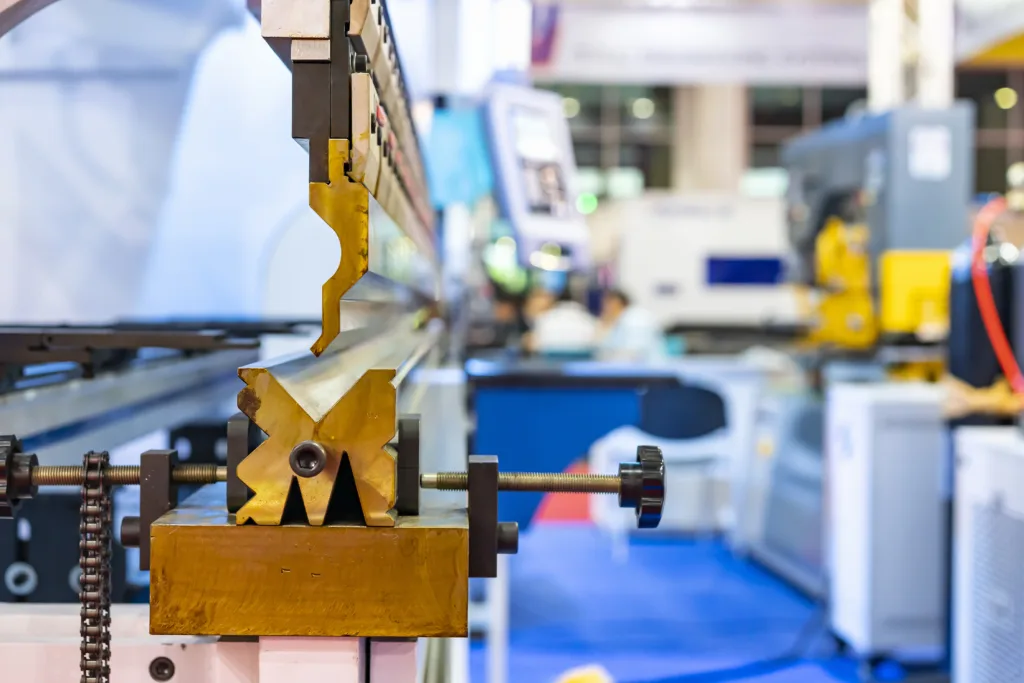
Perfect components in just 3 steps!
1
Make a request
Upload production drawing and specify order. You will receive your offer within 48 hours.
2
Quality control
We find the right paver, supervise production and take care of quality control in our in-house measuring center.
3
Components received
You receive your quality-tested components including detailed test certificate.
Prevent fractures
When does metal need hot and cold bending?
Most pieces of metal, especially thin plates or sheets, can be easily cold bent without prior heating. However, a few alloys require hot bending, as otherwise there is a risk of breakage.
For so-called hot bending, however, the metal plate is not actually heated to a high temperature before bending, but usually only heated. It is then shaped by the respective machine.
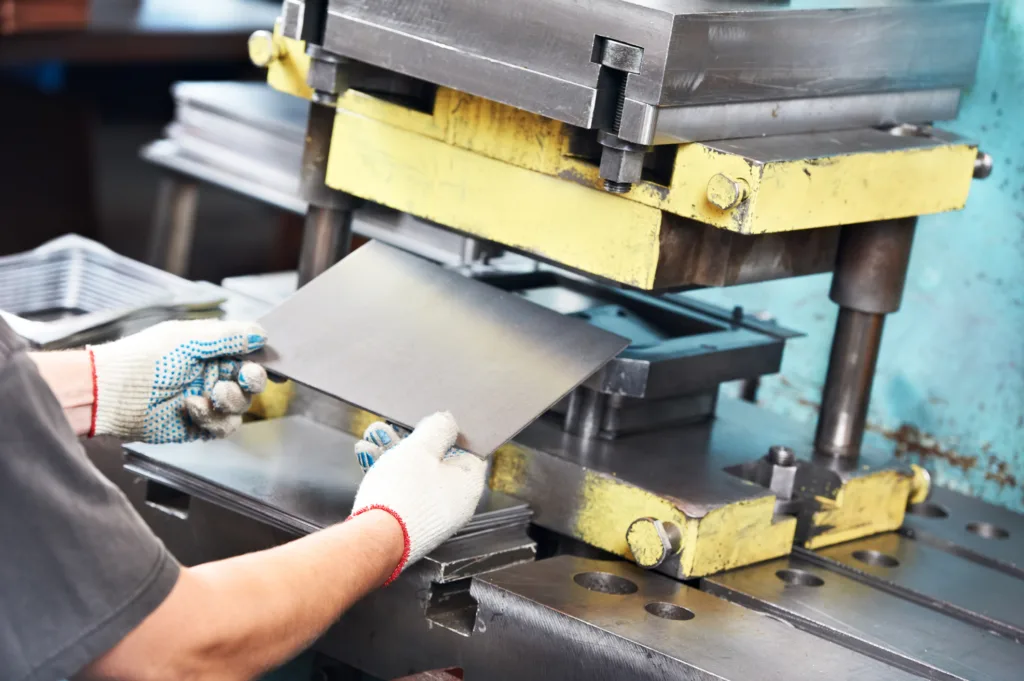
Get a quote for your parts
We will send you a suitable offer within 48 hours
Everything from a single source
Why not simply have sheet metal bent by an expert – CNC24
Many metal bending processes are extremely precise and economically viable. At the same time, however, metal forming is a professional craft that requires a lot of time and resources to produce in-house. You also need your own machinery.
Why not make it easy for yourself and let us bend your metal sheets?
CNC24 offers you a wide range of bending processes for metal such as die bending, swivel bending and roll bending. The precise bending of all common metals and alloys is one of our daily tasks.
Frequently mentioned disadvantages of contract manufacturing and how we have solved them at CNC24.
Does your planned component have an unusual shape? That’s no problem for us, we can shape your sheet metal into any desired form. We also offer other metalworking services if required. If it has to be done very quickly, even within 72 hours and without exception with a quality certificate.
Send us your request online today and you will receive your individual offer in just 48 hours.
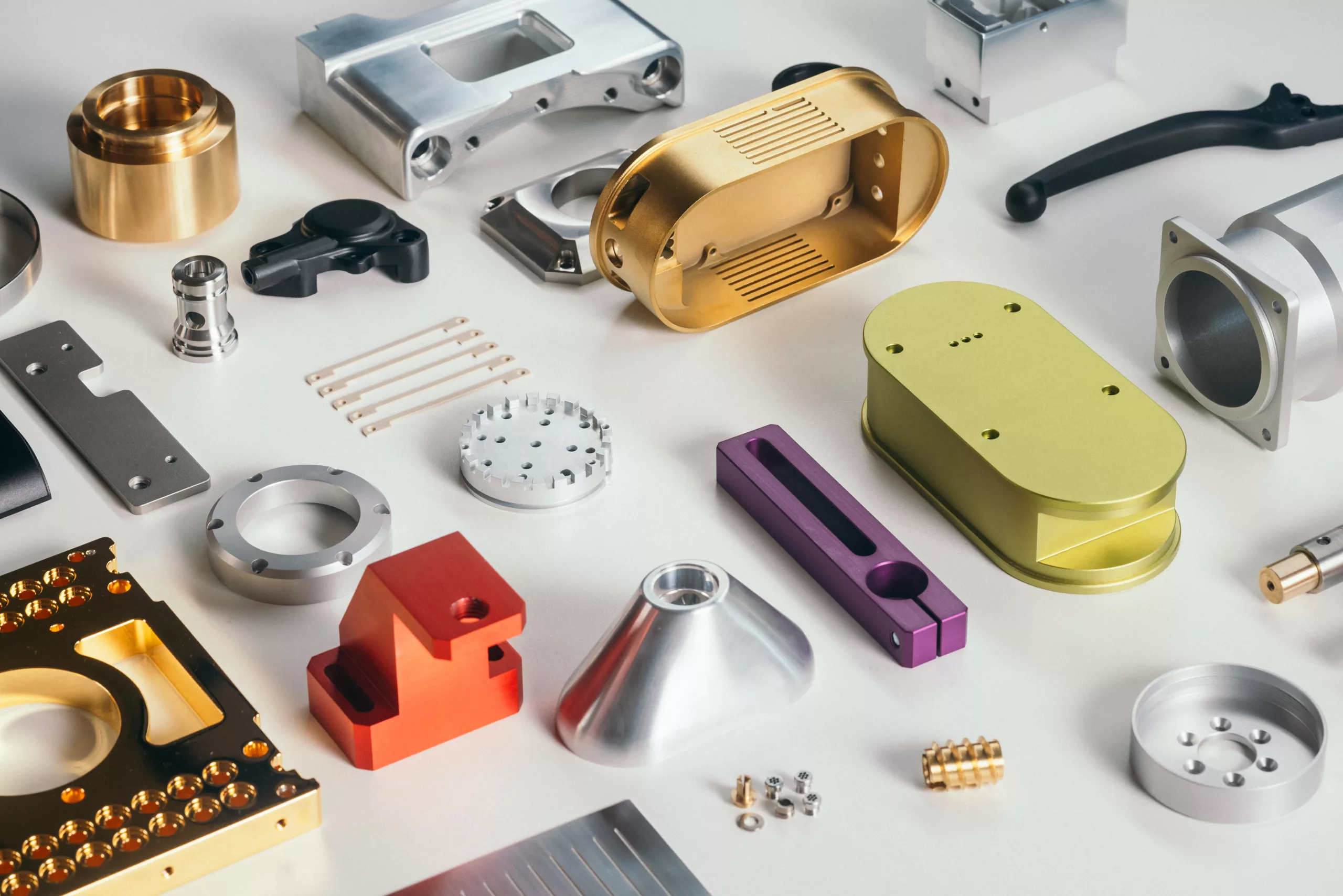
What we produce
Our sample components
Your partner for all components
Other manufacturing processes
CNC24
The easiest way to order components
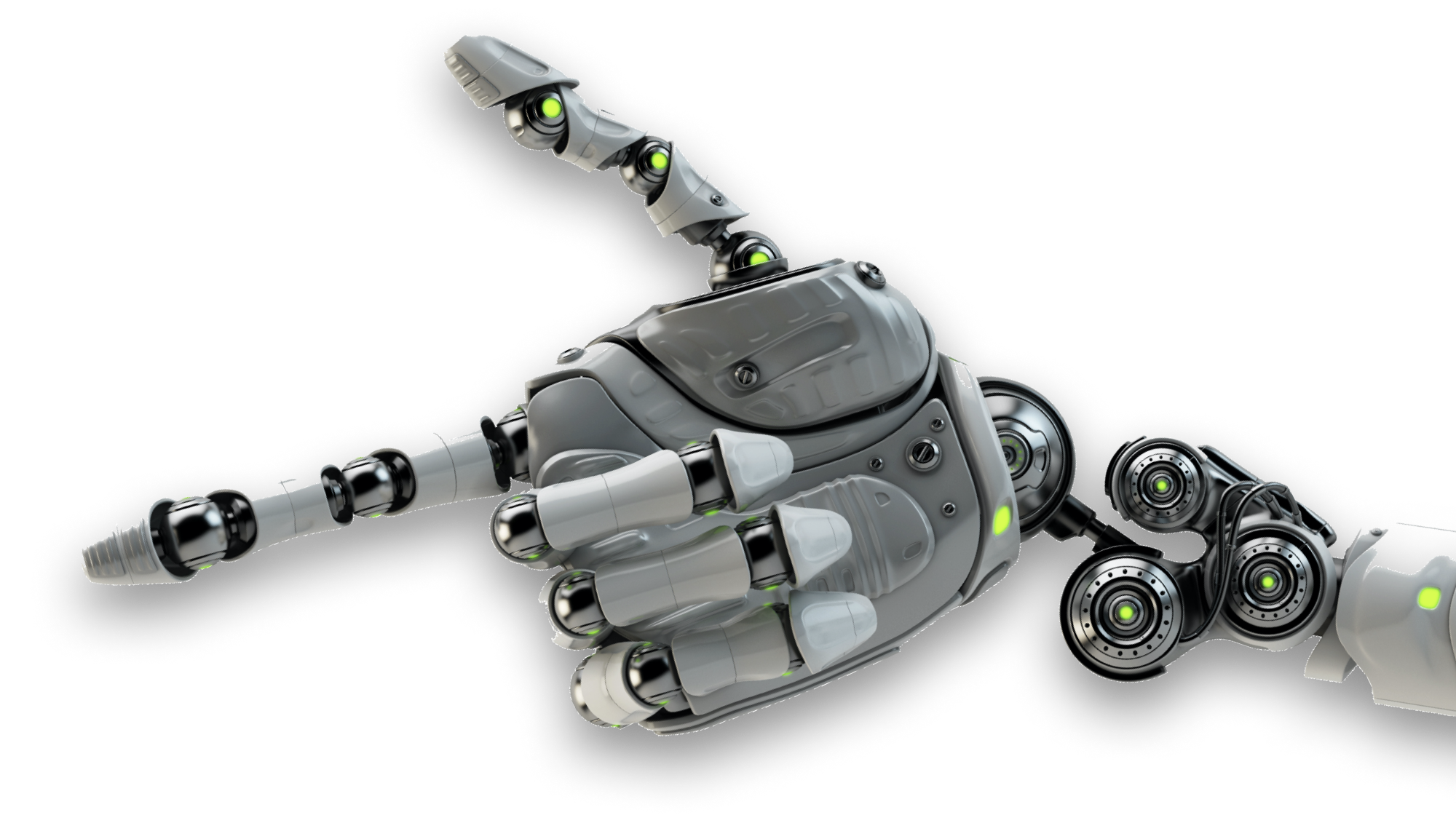