High precision thanks to automation and measurement technology
By networking all parties and using modern measurement technology, the CNC24 procurement platform ensures the quality of its precision components.
Quality plays a decisive role in the procurement of components. However, this presents companies with a major challenge. In order to find the right manufacturer to meet the requirements of the component, an extensive network of contract manufacturers is an advantage.
Especially when it comes to quality, price and delivery reliability. This is because machine manufacturers generally require thousands of different components for the manufacture of their products, for which reliable quality assurance is indispensable. Not every company in the industry has such a selection of supplier contacts to hand.
Procurement platforms such as CNC24 can be an important partner and the ideal complement to your own supplier network to ensure that a component is produced to the desired specifications and is of the best possible quality.
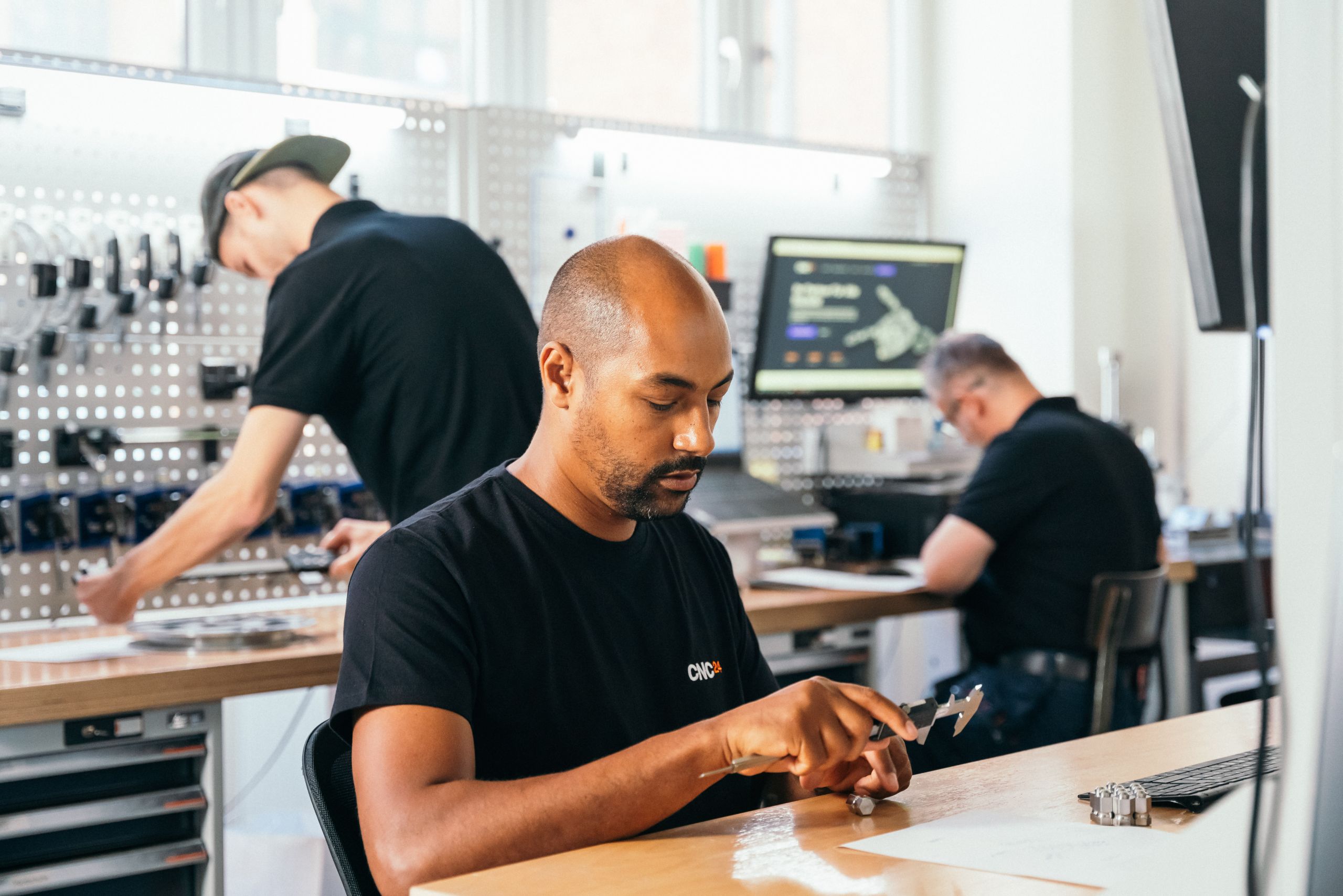
The process is based on the production drawing, from which all basic information and component requirements are automatically extracted. The component dimensions, materials, tolerances, the number of threads and thread types, information on the surface finish, revision number and test dimensions are read from it. All data points relating to a component are recorded and tracked digitally and automatically thanks to the digitized procurement process.
Customers upload 3D models and production drawings of the components to the customer portal so that production can be commissioned. All production-relevant information is automatically extracted from the production drawings. A combination of machine learning (ML) and artificial intelligence (AI) is used for this, which processes various drawing standards, file formats and languages. However, this is still not enough, as there are large deviations in the quality of the drawings when it comes to information and references – despite numerous standards in German industry. This is due to the fact that designers, purchasers and manufacturers have usually been in direct contact for many years, which means that a lot of information is only exchanged verbally or is part of the implicit know-how of a long-standing partnership. If this information is missing from the production drawing, the customer may be dissatisfied with the quality or production costs may increase due to unnecessary production steps.
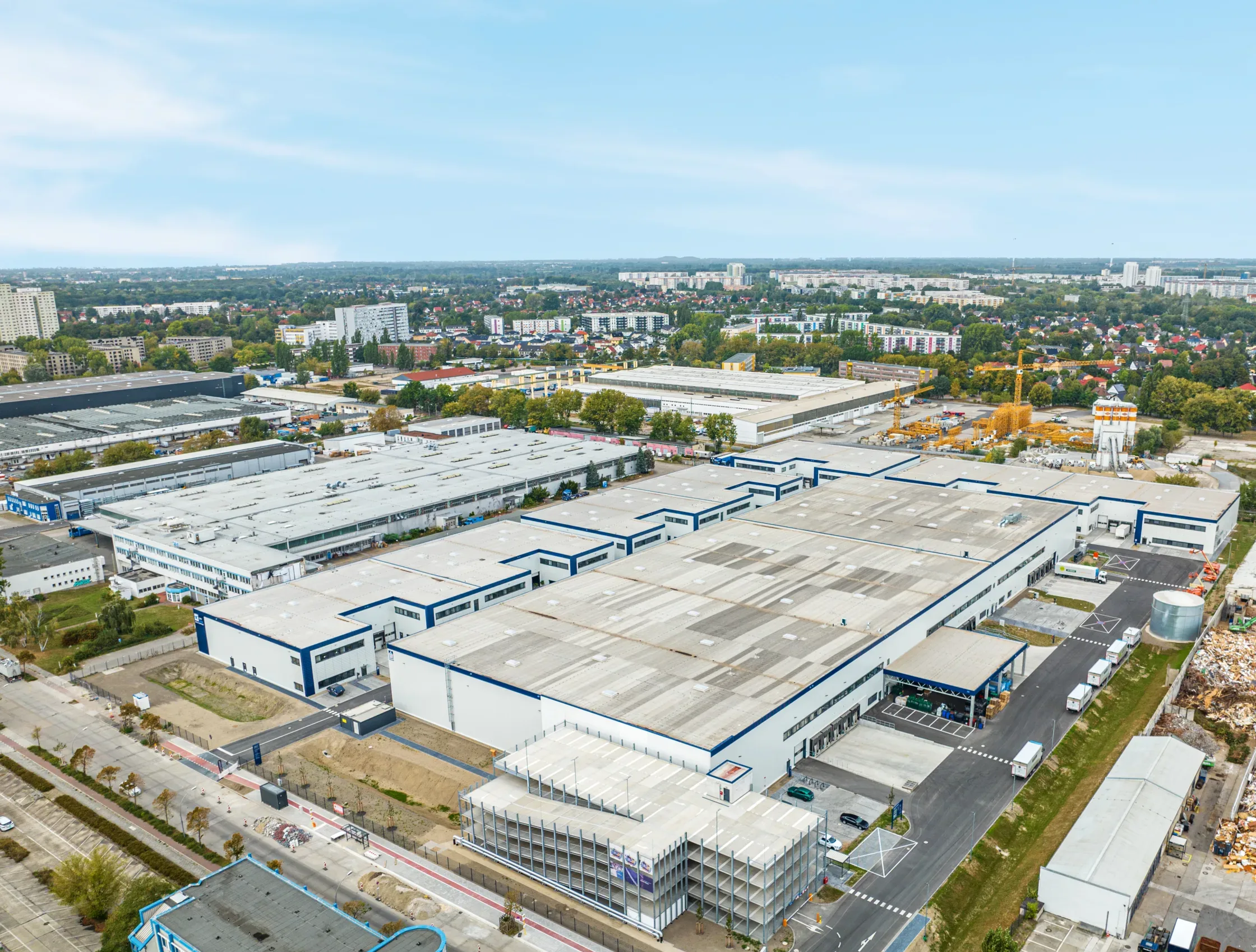
The tender to a paver is
paver is AI-supported
For example, it often happens that the value for the surface quality (Ra/Rz) is specified for the entire component surface, even if this would only really be necessary on one surface of the component. CNC24 therefore enriches the data in the production drawings with additional information supplied by the customer or, alternatively, determined by the customer himself when manually checking the drawings and inquiries. As soon as all the data on a drawing for a new order has been read out, supplemented and validated, the drawing is automatically anonymized and translated if necessary. Order-specific requirements such as a target price or an urgent delivery date can also be added. With the help of the AI-supported algorithm, the order is put out to tender to potentially suitable manufacturers. These include those whose skills, machine equipment and capacities best meet the customer’s requirements. All incoming bids are automatically evaluated and interpreted by the AI.
While some marketplaces use instant price calculators, CNC24 provides a quote within 48 hours. This guarantees the customer a suitable quote that meets all desired requirements and reflects a market-driven price. It also allows a great deal of flexibility in the quotation, as unlike an instant calculator, for example, only predefined materials or surface treatments are available for selection. If the customer decides to accept the offer, the procurement process begins.
Before the customer receives the components, the parts undergo an additional quality check at CNC24’s in-house measuring center in Berlin. Over 1000 components from more than 500 manufacturers are checked per month in an area of 1200m2. This ensures that the complaint rate is just 0.11%. The company uses measuring technology from Mitutoyo to check component quality in the measuring center: in addition to a large selection of manual measuring equipment, CNC24 also uses coordinate measuring machines, contour measuring devices, digital height gauges and surface inspection devices from Mitutoyo.
The focus here is on combining flexible quality inspection with digitalization. All measured values are transmitted digitally to ensure fast quality assurance processes. Each recorded component passes through the automated incoming goods department and is checked for all important features, such as quantity, appearance and packaging, using a checklist. The values determined during the measuring process are transferred wirelessly to the database via a system developed in-house. The digitally recorded component-specific characteristics are evaluated to identify error patterns and areas with optimization potential. Thanks to the high level of digitalization, suppliers receive a fully automated evaluation and targeted feedback on every order delivered.
CNC24 is now planning further automation steps and the construction of its first test center outside Germany.
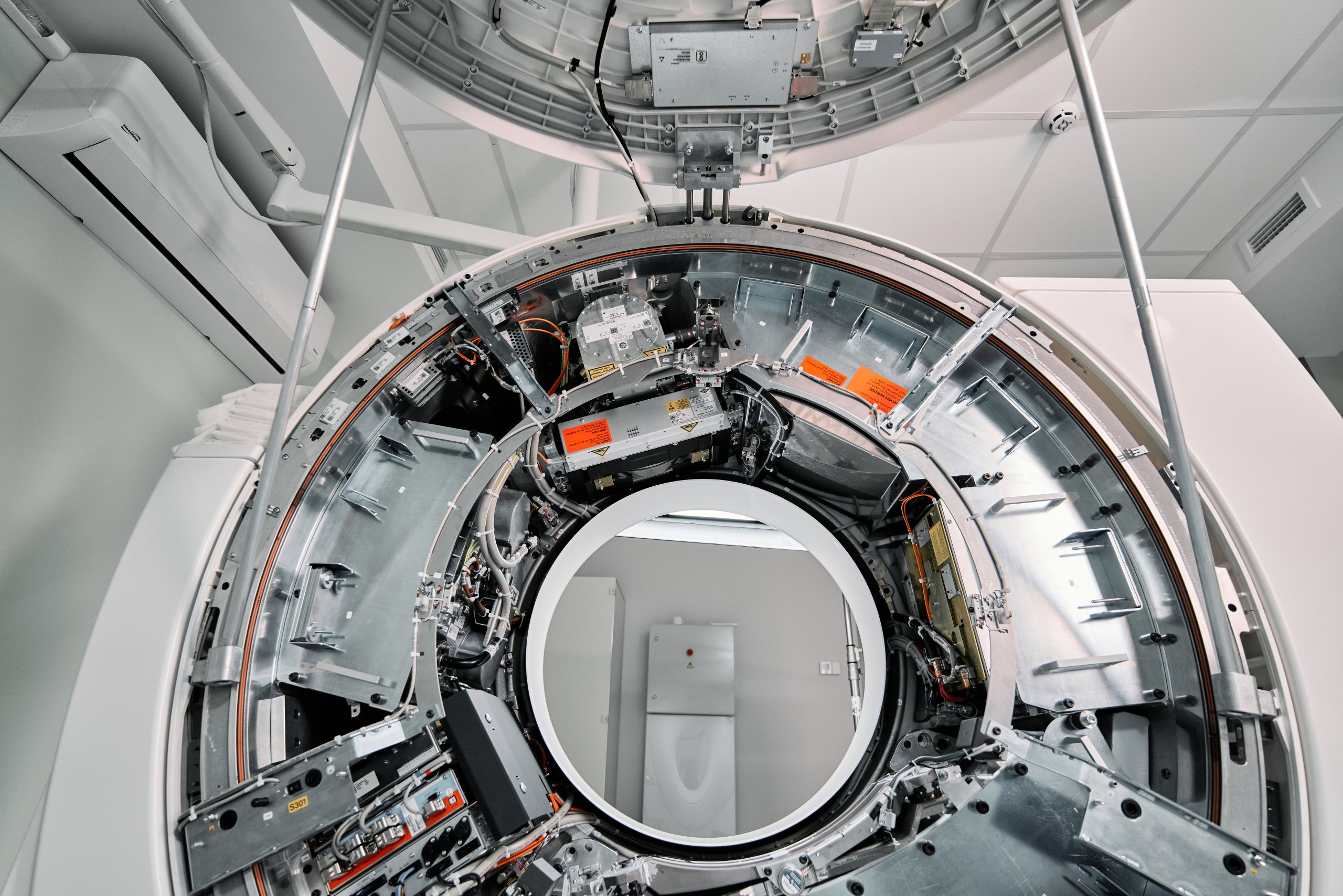
About CNC24:
CNC24 is a digital B2B procurement platform through which individual precision components can be sourced transparently and efficiently. Manufacturers from 22 countries produce the mechanical components individually according to customer specifications. The manufacturing processes offered by the leading online marketplace for mechanical engineering include turning, milling, sheet metal processing and additive manufacturing.
With its innovative platform solution, the technology company creates a transparent process for the procurement of production parts and digitalizes the value chain through to a fully automated procurement process. The company’s successful positioning as a partner for SMEs in terms of digitalization and innovation was confirmed in 2023 when it was awarded the German Excellence Award in the “Digital Startup Champions” category and the “Employer of the Future” seal. Thanks to its global network of suppliers, the company can guarantee free capacity, high material availability and on-time delivery of components at all times.
For quality control, all parts undergo an additional inspection process in the in-house measuring center before they are delivered. CNC24 was founded in 2019 by co-founders Willi Ruopp and Marlon Gerat.
The start-up serves all industrial sectors with a need for production parts – from special machinery and plant engineering to IOT, medical, testing and measurement technology. Its customers include well-known companies such as SIEMENS, DIEHL Group, Qualcomm, KRONES AG, Carl Zeiss, Vishay, BASF, CERN, FANUC, Syntegon, Jonas & Redmann, the Max Planck Institute and Fraunhofer.
More information at: www.cnc24.com
Press contact:
Linda Amamra
schoesslers GmbH
+49 151 722 25406
New CNC24 location from 01.02.:
City Dock Berlin Center
Marzahner Street 21
13053 Berlin
