ISO 9001 Certification as the basis for global supplier partnerships
Discover how ISO 9001 certification offers companies increased customer confidence, improved internal processes, international recognition, risk minimization and continuous improvement.
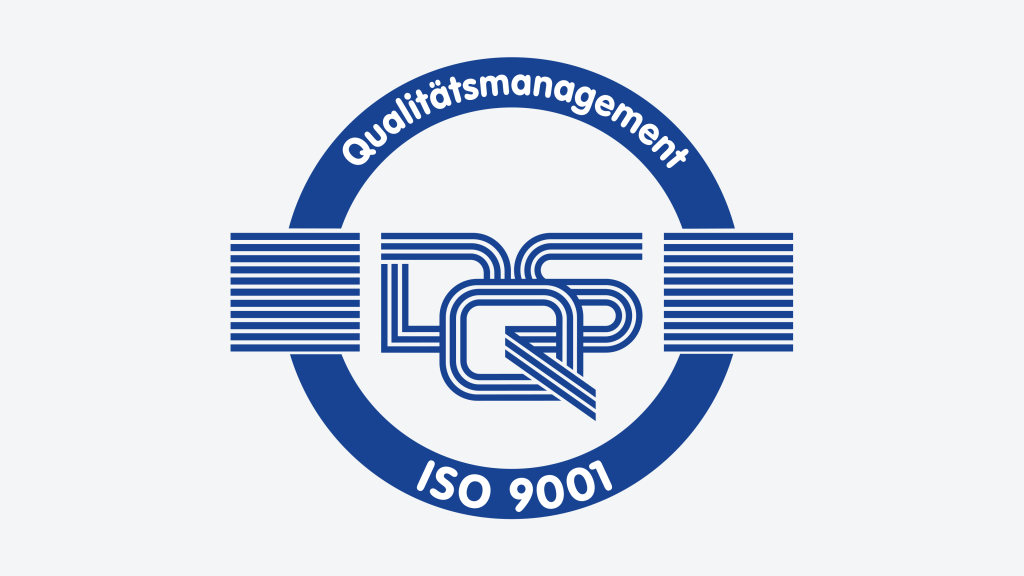
Discover how ISO 9001 certification offers companies increased customer confidence, improved internal processes, international recognition, risk minimization and continuous improvement.
Supplier selection on the basis of ISO 9001 Certification
In a globalized world where goods are often manufactured thousands of miles away, it is particularly important for companies to maintain high quality standards in their quest for success.
The ISO certification demonstrates the supplier’s commitment to maintaining German quality standards and complying with internationally recognized standards.
A mutual understanding of the scope of ISO 9001 certification enables companies to make an informed decision when selecting suppliers.
What is ISO 9001?
ISO 9001 is an internationally recognized standard for quality management systems.
Certification provides a framework to help companies establish and maintain processes to ensure consistent quality and customer satisfaction.
ISO 9001 defines criteria for a quality management system, including a strong customer focus, continuous improvement and a process-oriented approach.
The certification serves as a testimony to a company’s commitment to meeting customer requirements and delivering products or services of the highest quality.
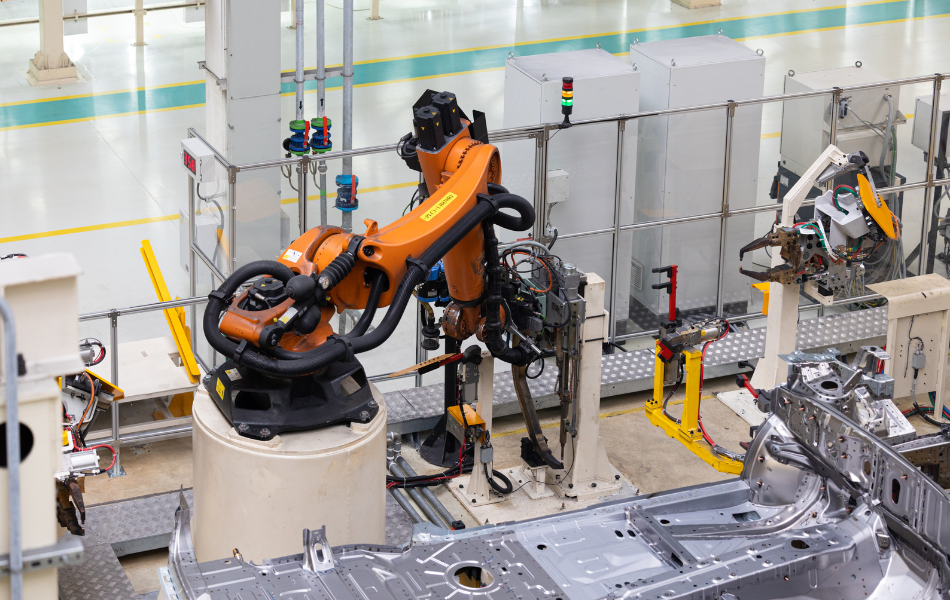
What advantages does ISO 9001 offer?
Obtaining ISO 9001 certification offers numerous advantages to both the supplier and the buyer. Some of the most important advantages are
- Increased customer confidence: ISO 9001 certification demonstrates a supplier’s commitment to meeting customer requirements and delivering superior products or services. Certification gives potential buyers confidence and assures them that the supplier is focused on quality.
- Improved internal processes: Implementing ISO 9001 requires organizations to establish effective processes and procedures. This helps to optimize processes, eliminate inefficiencies and reduce errors. By adhering to standardized processes, the supplier can consistently deliver high-quality products and services, which benefits both the buyer and their own company.
- International recognition: ISO 9001 is internationally recognized and respected. Working with a supplier that has this certification offers a strong competitive advantage, especially in a globalized market environment. The certification is a testament to the supplier’s commitment to meeting the highest quality standards.
- Risk minimization: ISO 9001 certification places particular emphasis on risk management and encourages companies to identify potential risks and take preventative action. This proactive approach helps to minimize risks and address potential quality issues before they impact the buyer’s business operations or reputation.
- Continuous improvement: ISO 9001 promotes a culture of continuous improvement. Certified suppliers are required to regularly monitor and evaluate their processes to identify opportunities for improvement. This commitment to continuous improvement benefits both the supplier and the buyer by encouraging innovation and ensuring a constant focus on quality.
Steps to ISO 9001 Certification
Obtaining ISO 9001 certification involves a systematic process. While the specific steps may vary depending on the organization, the general framework usually includes the following:
- Gap analysis: The supplier evaluates its existing quality management system against the ISO 9001 requirements and identifies areas that require improvement.
- Documentation development: The supplier shall develop and document its quality management system, including policies, procedures and work instructions, to ensure compliance with ISO 9001 standards.
- Implementation: The supplier implements the documented quality management system throughout the organization, trains employees and ensures compliance with the defined processes.
- Internal audits: Internal audits are conducted to evaluate the effectiveness of and compliance with the quality management system. This step helps to identify any gaps or deviations that need to be rectified.
- Management review: Top management reviews the performance of the quality management system and ensures that it remains appropriate and effective.
External audits: An accredited certification body carries out an external audit to assess compliance with the ISO 9001 requirements. If the audit is successfully completed, ISO 9001 certification is awarded.
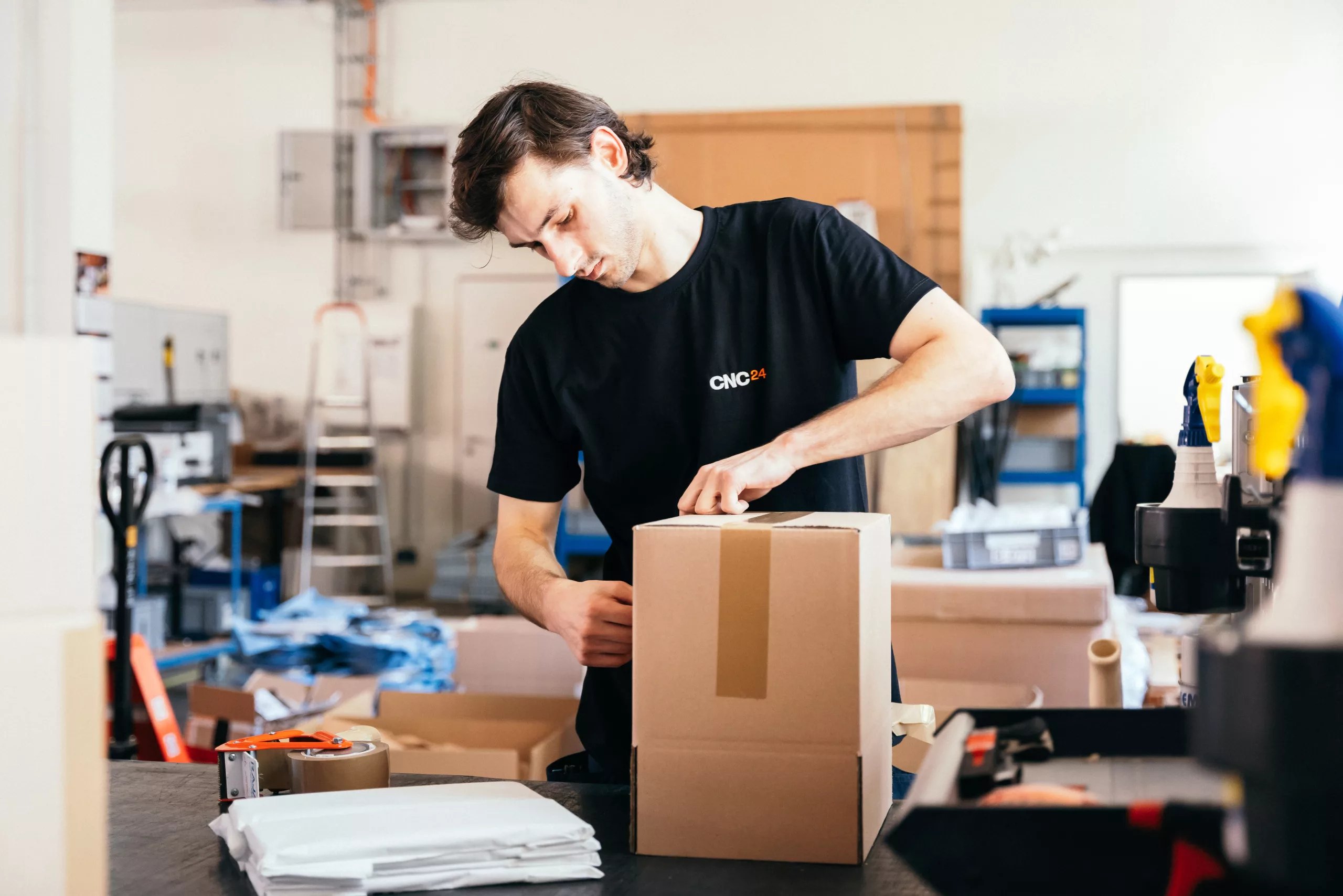
ISO 9001 Certification Process
Step | Description |
1 | Carrying out a gap analysis to identify areas for improvement in the current quality management system. |
2 | Development and documentation of the quality management system, including guidelines, procedures and work instructions. |
3 | Implementing the quality management system throughout the organization, ensuring compliance and training employees. |
4 | Conducting internal audits to evaluate the effectiveness of and compliance with the quality management system. |
5 | Top management reviews the performance of the quality management system and ensures its continued suitability and effectiveness. |
6 | An accredited certification body carries out an external audit to assess compliance with ISO 9001 requirements. |
7 | ISO 9001 certification is awarded on successful completion of the external audit. |
What is a quality management system?
At the heart of ISO 9001 is the concept of a quality management system. A quality management system (Q MS) is a set of interrelated processes and procedures that an organization establishes to achieve its quality objectives. It provides a framework for the consistent delivery of products or services that meet customer requirements and improve customer satisfaction.
A robust QMS helps organizations identify, document and monitor key processes to ensure they are performed effectively and efficiently. It includes various elements such as process management, resource allocation, performance measurement and continuous improvement.
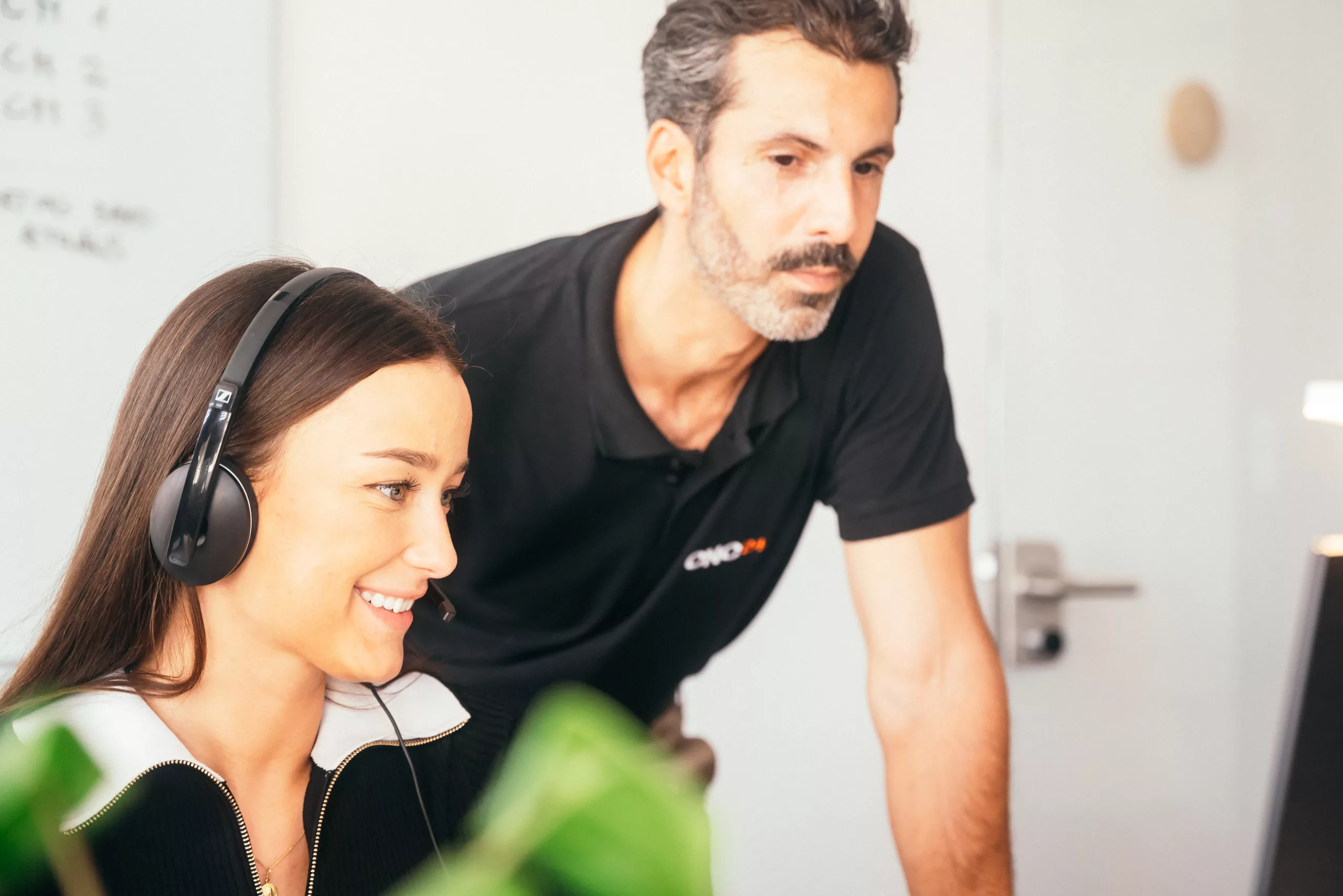
Good reasons for a quality management system
The implementation of a QMS according to ISO 9001 requirements brings several concrete advantages for the supplier. Some of these benefits are
- Improved organizational efficiency: A well-defined QMS ensures that processes are optimized, redundancies are reduced and efficiency is increased. This leads to an optimized use of resources and improved productivity.
- Consistent product/service delivery: By standardizing processes, a QMS enables suppliers to consistently deliver products or services that meet predefined quality standards. This consistency creates trust with customers and promotes long-term relationships.
- Improved risk management: A QMS facilitates the identification, assessment and minimization of risks. Through proactive risk management, suppliers can minimize the occurrence of quality problems and ensure smooth processes for the buyer.
- Increasing customer satisfaction: ISO 9001 promotes a customer-oriented approach and helps suppliers to better understand customer requirements and to meet or exceed them. This focus on customer satisfaction strengthens relationships and promotes customer loyalty.
- Promote continuous improvement: A QMS encourages organizations to adopt a continuous improvement mindset. By monitoring processes, collecting data and analyzing performance metrics, suppliers can identify opportunities for improvement and drive innovation.
Get a quote for your parts
Why is a process-oriented approach important for ISO 9001 certification?
ISO 9001 places particular emphasis on the introduction of a process-oriented approach within an organization. This approach focuses on understanding and managing the interrelated processes that contribute to the achievement of quality objectives. The process-oriented approach has several advantages:
- Transparency of departments: By adopting a process-centric approach, organizations gain a clear understanding of the connections between their departments and the processes implemented. This promotes transparency and enables companies to identify bottlenecks, optimize workflows and allocate resources efficiently.
- Identification of process inputs and outputs: The process-oriented approach requires organizations to define inputs, activities and outputs for each process. This clarity ensures that each step in the process is well documented and meets quality objectives.
- Continuous monitoring and improvement: Implementing a process-oriented approach enables organizations to monitor the performance of processes and measure key indicators. This data-based approach facilitates the identification of improvement opportunities and drives continuous development.
- Identification and minimization of risks: By mapping out processes, organizations can identify potential risks and develop appropriate control measures. This proactive approach to risk management minimizes the occurrence of quality issues and helps maintain high standards.
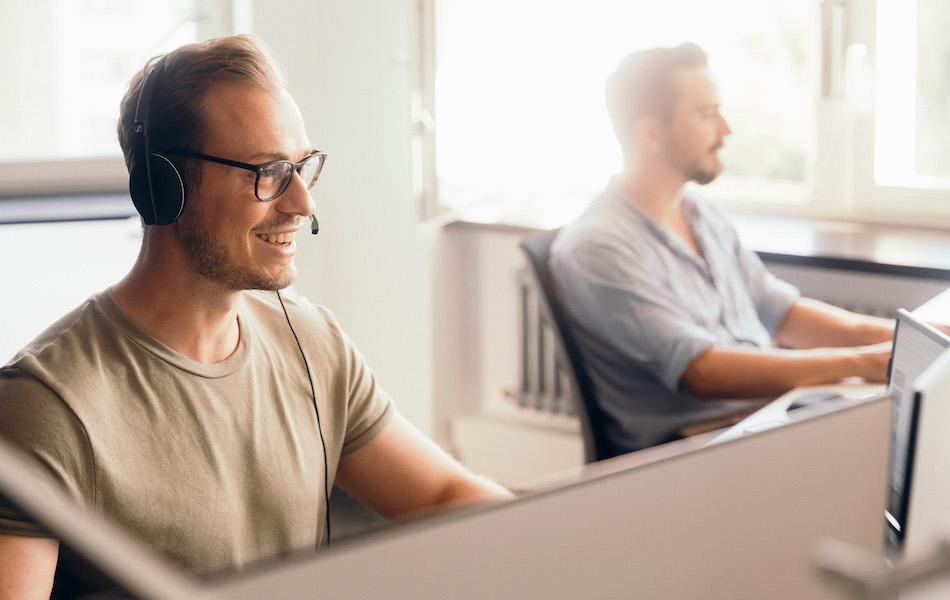
Main Advantages of ISO 9001 Certification
Advantage | Description |
Improved customer confidence | ISO 9001 certification demonstrates a commitment to meeting customer requirements and delivering high quality products or services. |
Improved internal processes | The implementation of ISO 9001 helps to optimize processes, eliminate inefficiencies and reduce errors. |
International recognition | ISO 9001 is internationally recognized and offers a competitive advantage on the global market. |
Minimized risks | ISO 9001 certification places great emphasis on risk management to proactively identify and address potential quality issues. |
Continuous improvement | ISO 9001 promotes a culture of continuous improvement and innovation. |
Summary
A global supplier partnership with ISO 9001 certification offers significant advantages for companies that place great value on high-quality products or services. ISO 9001 ensures compliance with German quality and sets high standards for the supplier’s internal CNC manufacturing processes. By choosing a certified supplier, companies can expect increased customer confidence, improved internal processes, international recognition, risk minimization and continuous improvement.
The steps to ISO 9001 certification include a gap analysis, the development of a quality management system, implementation, internal and external audits and obtaining certification.
Implementing a quality management system in accordance with ISO 9001 requirements offers several tangible benefits for a supplier: including improved organizational efficiency, consistent product/service delivery, improved risk management, increased customer satisfaction and continuous improvement.
A process-oriented approach is important for ISO 9001 certification because it creates transparency, identifies process inputs and outputs, enables continuous monitoring and improvement, and supports effective risk identification and minimization.
Through ISO 9001 certification, companies can build a solid foundation for success in the global marketplace and ensure that they deliver on their promises of quality and customer satisfaction.
Download Industry Paper
Survey on the Status of Component Procurement
Download Industry Paper
We have structured the most important findings for you and presented them clearly in an industry paper.
Please note that the survey is only available in the German language.
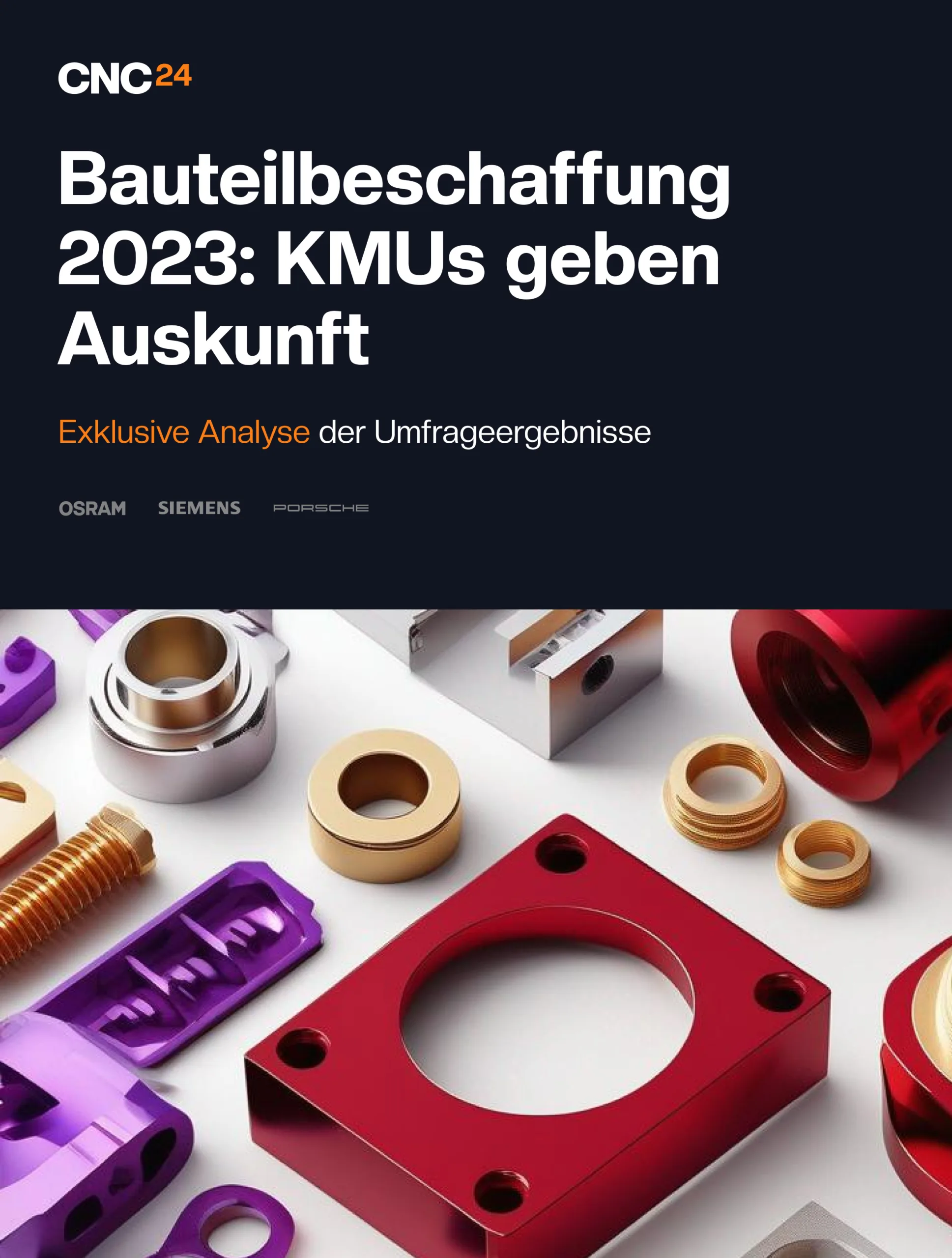
Get a quote for your parts
About CNC24
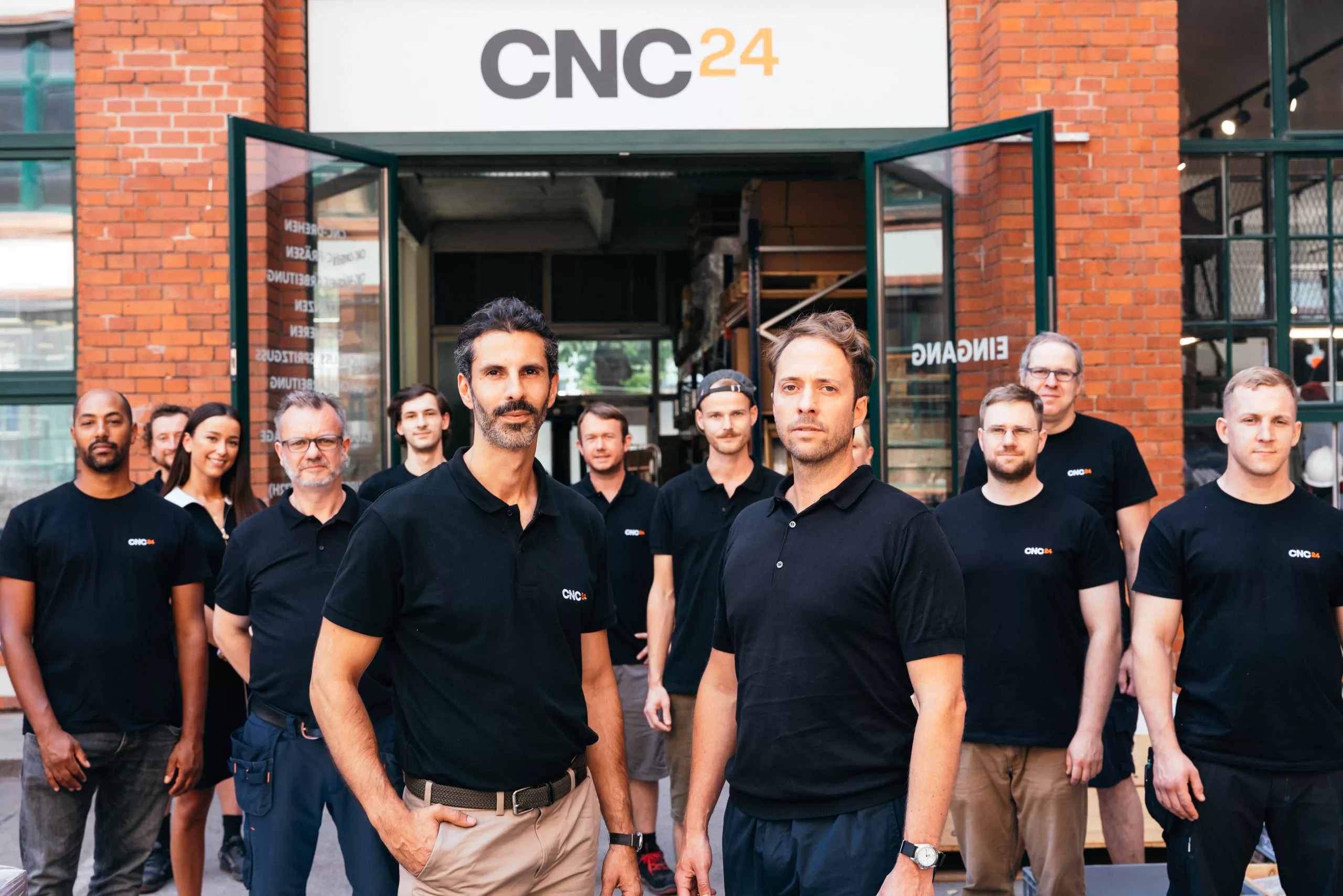
CNC24, a brand of CNC24 GmbH, is a digital B2B procurement platform through which individual precision components can be sourced transparently and efficiently.
Manufacturers from 22 countries produce the mechanical components individually according to customer specifications. The manufacturing processes of the leading online marketplace for mechanical engineering include turning, milling, sheet metal processing and additive manufacturing.
With its innovative platform solution, the technology company creates a transparent process for the procurement of production parts and digitalizes the value chain through to a fully automated procurement process.
The company’s successful positioning as a partner for SMEs in the field of digitalization and innovation was confirmed in 2023 when it was awarded the German Excellence Award in the “Digital Startup Champions” category and the “Employer of the Future” seal. Thanks to its global network of suppliers, the company can guarantee free capacity, high material availability and on-time delivery of components at all times.
For quality control, all parts undergo an additional inspection process in the in-house measuring center before they are delivered. CNC24 was founded in 2019 by co-founders Willi Ruopp and Marlon Gerat. The start-up serves all industrial sectors with a need for production parts – from special machinery and plant engineering to IOT and medical, testing and measurement technology.