3D printing with metal-process & application explained
The 3D metal printing process is currently the most innovative and fascinating technology on the market.
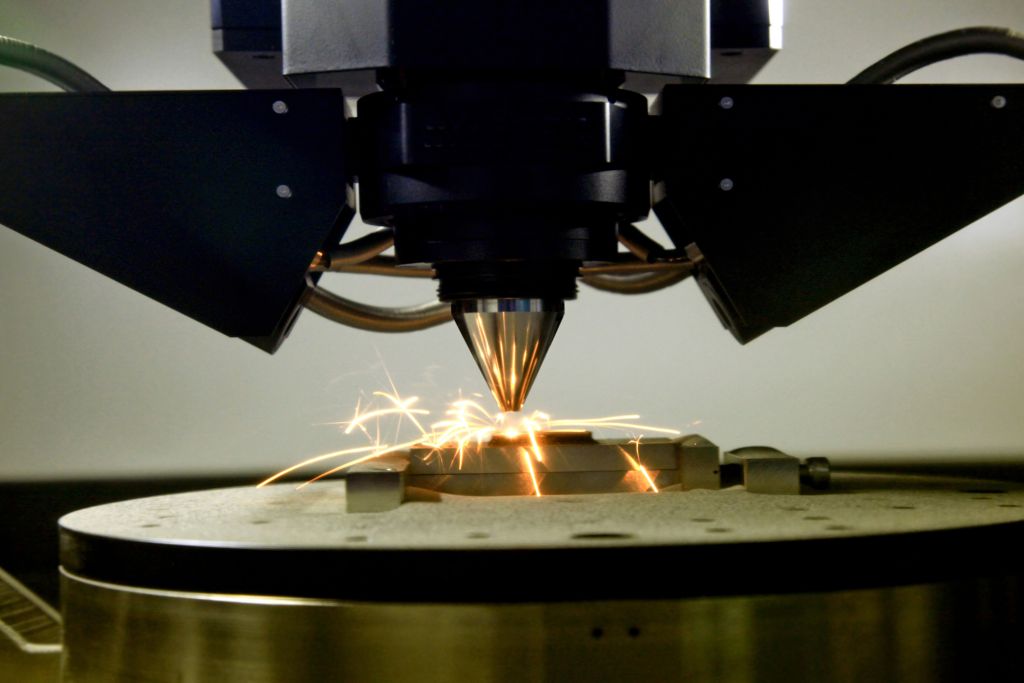
The 3D metal printing process is currently the most innovative and fascinating technology on the market. There is hardly a branch of industry that cannot benefit from this process technology. Are you thinking about switching your production to 3D printing?
Then this article is for you. In it, we describe interesting background information on the topic and provide you with an overview of the most important metal printing processes. We also provide information on the advantages and possible disadvantages of 3D printing in metal. You will find out in which industries 3D printing technology has already established itself and how a model is produced in 3D.
How does 3D printing with metal work?
The term 3D printing is a collective term and describes a collection of additive manufacturing techniques in which material is layered to create a three-dimensional workpiece. Below you will find an overview of the four most important 3D printing processes.
Fused Deposition Modeling (FDM)
This process is primarily used for the production of functional prototypes and tools. A plastic wire (filament) is melted in the so-called hot end of the printer and then returns to the print bed layer by layer. The material then hardens again.
Materials suitable for the FDM method:
- PLA (Polyactic)
- PVA (polyvinyl alcohol)
- HIPS (High-Impact Polystyrene)
- PET (polyethylene terephthalate)
- Nylon
- Filaments based on e.g. metal, stone, wood
Polyjet process (Multijet Modeling MJM)
In multi-jet modeling, tiny droplets of a photopolymer are applied to a platform using a print head. This is then placed under UV light where it hardens. Not only can different materials be used in the polyjet process, they can even be mixed. This and the possibility of processing wafer-thin layers of up to 14 μm make the polyjet process very popular for the production of individual prototypes.
Stereolithography (SLA)
Anyone aiming to produce complex geometric components is well advised to use SLA. This method is based on a tank filled with resin (photopolymer resin). Photosensitive material can be used. This is cured using a UV laser and the platform is lowered. This process now takes place layer by layer, and the support structures used produce astonishingly precise results.
Selective laser sintering (SLS)
Prototypes and finished components can also be produced using the SLS process. This is a powder-bed-based 3D printing process. The SLS 3D printer forms components using selective laser sintering. Each layer is also applied individually. Accurate results are also guaranteed with this method.
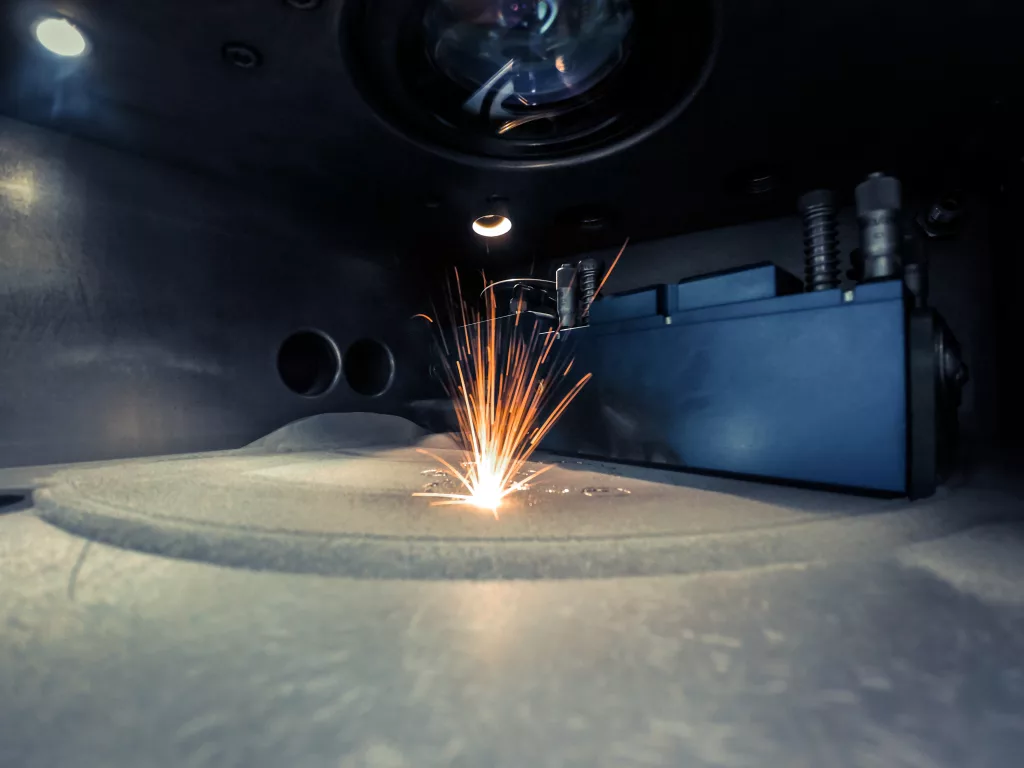
What are printed metal objects needed for?
A wide range of industries benefit from the innovative technology of the 3D metal printing process. Here are a few examples:
- Automotive industry
Additive manufacturing technology became established in the automotive industry some time ago. Prototypes as well as end parts and spare parts are successfully produced with it. By far the largest customer base for metal parts in 3D printing is in motorsport.
One reason for this is that the use of 3D metal printers can save a significant amount of time and money while maintaining the same level of quality. Furthermore, complex properties of individual components can generally be implemented quickly. The number of cooperation partnerships in the field of 3D printing in amateur and professional motorsport is growing steadily. In addition, 3D metal components are used in the restoration of classic cars, whose defective components would otherwise be difficult to access.
- Aerospace industry
The lightweight construction of 3D metal printing components is of crucial importance for the aerospace industry. The process is used to produce prototypes as well as parts and components for launch vehicles, satellites and transport vehicles, among other things.
Even if high-quality 3D metal printers can easily eat up a budget of around a million euros, aviation institutions say they pay for themselves thanks to their low material wear, short production time and excellent material strength compared to conventional manufacturing methods.
- Industry and trade
3D metal printing is also a popular process method in tool manufacturing. Various industrial tools can be equipped with additional functions and can therefore make other production applications faster and more economical. Even within this industry, the long-term improvements in performance justify the high acquisition costs of 3D devices.
For example, the production of metal molds with internal, uniform cooling channels using DMLS/SLM 3D printing is popular. An even more cost-effective alternative for the production of modern 3D printed components can be to outsource production to professional production workshops such as CNC24. This completely eliminates the need to purchase a 3D printing device. We would be happy to advise you on your individual wishes and requirements for your project.
- Medical and biomedical industry
3D metal printers are also able to create organic structures. The production of customized prostheses and implants is one of the main areas of application of the 3D printing process in medicine today. Biocompatible materials such as titanium are used for this purpose.
Surgeons also use 3D models for training and surgery preparation. They are regularly used in the USA in particular and are intended to reduce medical errors in the future. The models can also be used as illustrative material for patients. Biomedicine is in the ongoing research phase of printing human organs and stem cells.
- Research and innovation
For research, the invention of 3D printing was and is a major step towards the future. Printing process technologies, such as metal extrusion, are time-saving. In some cases, they shorten market launch processes many times over compared to traditional and in-house options.
Furthermore, thanks to 3D metal printing technology, innovations are possible that would have been beyond our imagination in the last decade. For example, according to the latest news from 3D Grenzenlos magazine, researchers have succeeded in developing a 3D drug printer. Printed medicines tailored to the patient allow the release of active ingredients into the body via specific geometries or surfaces. The printer could bring further advantages in precision medicine, among other areas.
Get a quote for your parts
Which metals can be used for metal printing?
In principle, a wide range of metal 3D printing processes are available to you. CNC24 offers you stainless steel, bronze and copper for processing. Due to its lightness and robustness, we can also recommend aluminum alloys in particular for prototype production. In most cases, 3D printing involves aluminum alloys.
We also offer titanium in 3D printing. Titanium is biocompatible and is therefore often used in medical technology, among other things. In addition, printed titanium parts have good mechanical properties. They can be produced in a single batch, eliminating the need for sensitive welding steps for the metal.
Otherwise, Inconel is a material that is ideally suited to the production of 3D prints. It has exceptionally good heat resistance and is highly resistant to corrosion. For these reasons, Inconel is often used in 3D printing in the automotive and aerospace industries for functional prototypes and high-performance components.
Available metal materials at CNC24
- Aluminum
- Stainless steel
- Bronze
- Copper
- Inconel
- Titanium
The material of your choice is not listed? Please contact us if this is the case. Thanks to our large partner network, the chances are very good in most cases that we can procure it for you as quickly as possible.
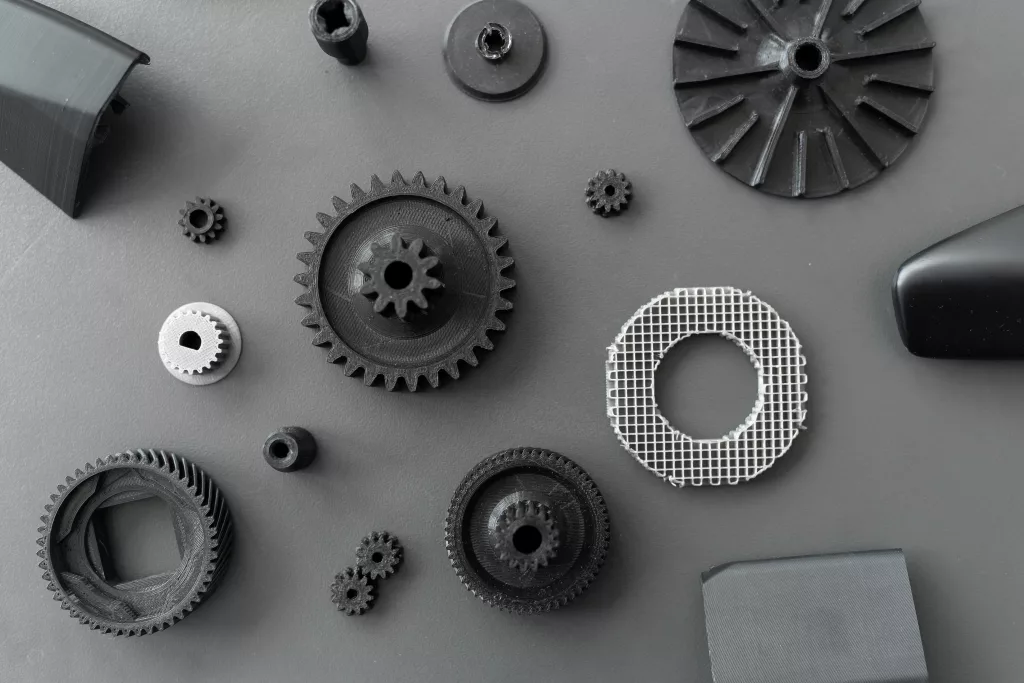
Why should you opt for metal 3D printing?
One of the biggest advantages of the 3D metal printing process is the ability to create complex and intricate shapes and geometries in a comparatively short time. Even cavities and undercuts are no problem and a high-quality, process-oriented design is possible. Another advantage is that it is a tool-free production process and material consumption is much lower than with conventional methods.
Even bionic structures are possible with 3D printing technology and, overall, we can speak of customer-oriented production in all sectors. The latter means that there are shorter supply chains. The modern process technology is intended in particular for the production of individual components and small batches. A production method that primarily takes place on-demand also creates a sustainability factor that should not be neglected.
The biggest advantages of 3D metal printing at a glance
- Low material consumption
- Complex shapes and geometries possible
- Creation of aesthetic design and finish
- Functional improvements of components possible
- Subsequent adjustments are possible
- Customer-oriented production
- Increasing cost-effectiveness (for smaller quantities and complexity)
- No tools required
- diverse possibilities in lightweight construction technology
- Possibility of designing components in line with the process
- High potential for research and product development
Are there any restrictions with 3D printing?
The printing process is generally not designed and made for large series production. This is mainly due to the fact that a 3D printer has a relatively low build-up speed. A 3D metal printed part takes at least 48 hours or an average of around five days to finish. Post-processing may also be required, especially when it comes to the production of complex formations – but this can also be a decisive advantage for complex prototypes.
Furthermore, a specialist is required to decide which 3D metal printing process is the right one for the job in question based on the material properties. A 3D metal printer is cost-intensive, which is why many companies decide to outsource this task to a team of experts.
How do you design models for 3D printing?
To prepare the design for 3D metal printing, you should take a close look at the desired design. In principle, the preliminary design of a 3D print is initially comparable to that of other manufacturing techniques. However, the special thing is that you are not restricted and can actually implement complex designs down to the last detail. Make the most of this advantage, as this is one of the main benefits of this process technology.
However, it is important to know that parts that have already been produced using traditional methods cannot simply be transferred 1:1 to 3D printing. This often results in manufacturing errors and also often restricts your design. Optimizations for existing workpieces are another matter. When 3D printing, start with an empty work surface. Then define your design requirements in detail. This includes loads, boundary conditions, part weights and more.
The print orientation is also decisive for the position of the support structures, which you should be able to determine. The creation of parts with self-supporting features and consequently minimal support structures is advantageous at this point. Furthermore, when designing a model, you should always bear in mind that optional or necessary post-processing will be necessary in many cases.
Design software in metal 3D printing
For 3D designs, CAD packages such as Altair, Autodesk Fusion 360 or nTopology Element are available to help you with planning. Modern algorithms make it possible to create organic structures. You can now also start your own new design and begin with the basic structure and the input of requirements or edit or optimize an existing one.
- Grid pattern
Would you like to optimize an existing design? Then grid patterns are the right choice. They can be used to improve printability, increase the surface area of heat exchangers and optimize manufacturing costs. - Topology optimization
Do you have minimal mass and want a structure with optimum rigidity? Would you like to push the desired parts to their load limits and subject them to the ultimate test? Then simultaneously controlled topology optimization is the ideal solution. It analyzes your input with regard to the design space and the load cases. In this way, the system determines where material can be removed. - Generative design
Here we are talking about a variant of the topology optimization process just mentioned. Generative design leads to different design variants, all of which would meet his requirements. They can then be printed out, extensively tested and compared by the designer at his leisure.
Do not underestimate modeling for 3D printing and make sure that CAD packages are up-to-date and of high quality when purchasing them. Designing 3D elements for metal printing is complex and only recommended for non-professionals to a very limited extent. In some cases, even professionals have to tinker for a long time to achieve the optimum result. An experienced professional like CNC24 takes a lot of the work off your hands while you can continue to focus 100% on your day-to-day business.
Get a quote for your parts
Why CNC24 is your best contact for metal prints
3D printing with metal is probably one of the most impressive process technologies currently available and offers companies many opportunities across all industries. At the same time, however, the process is very complex and requires a high level of expertise, particularly in the professional printing sector.
Just leave your work to us!
CNC24 is the right place for you if you are looking to manufacture prototypes or small series using 3D printing with rapid availability. This is precisely our focus in this manufacturing process. Our service offers precision and replicability for your desired components. We support you in rapid prototyping, rapid tooling and the production of small series.
Our 3D printing processes at a glance
- Polyjet (MJM)
- Selective laser sintering (SLS)
- Selective laser melting (SLM)
- Fused Deposition Modeling (FDM)
- Multi Jet Fusion (MJF)
- Stereolithography SLA
3D printing technical data
- Material thickness: 0.1 mm – 10 mm
- Available lengths: 10 mm – 2,000 mm
- Tolerances: +/- 0.1 mm to +/-1 0.3 mm
- Surface quality: 3.2 Ra µm
- Ideal batch sizes: 1 – 50,000 pieces
What you can expect from us
CNC24 stands for flexible and free capacities as well as attractive prices at all times. A personal contract and contact person is available to you throughout the entire project. Quality control in accordance with ISO 9001:2015 is a matter of course for us. And if time is of the essence, we also offer express production within the respective process technology and up to 72 hours.
In addition to 3D metal printing, we also use other process technologies such as die-casting and injection molding as well as various CNC techniques such as CNC turning. Combination offers are possible.
See for yourself and request your personal quote today. We will send you a quote within 48 hours of receiving your request. Do you have any questions? Our team will be happy to assist you by telephone on +49 (0)30 994 04 904.
Optimization of your supplier search
Download Whitepaper
Find out now which 9 points you should consider so that you can find the right supplier and reduce your costs by up to 40%.
Please note that the whitepaper is only available in the German language.
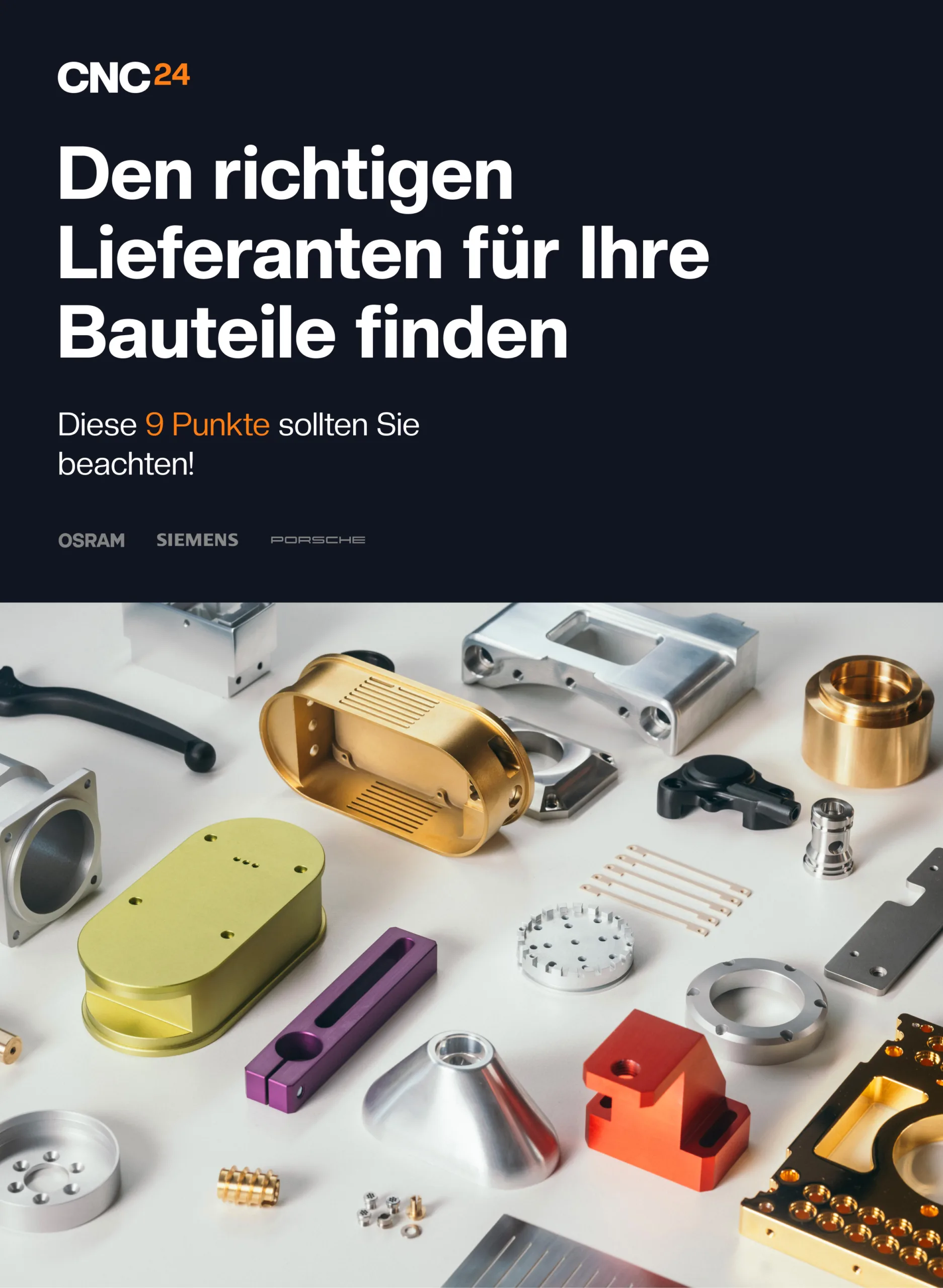