Precise welding with TIG process
TIG welding is the abbreviation for tungsten inert gas welding. This is welding with a shielding gas.
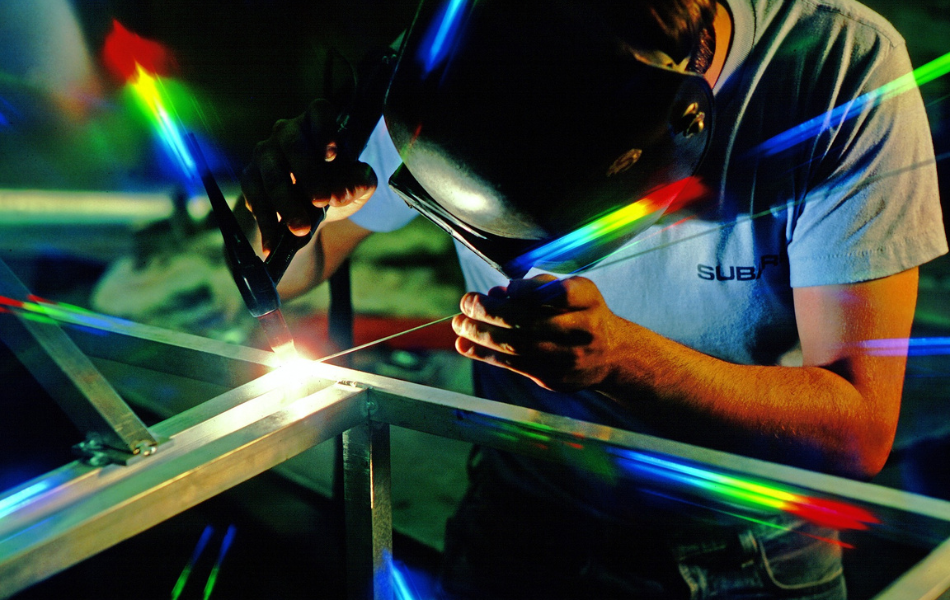
Are you looking for a welding process that can not only produce high-quality work, but that you can also expect to look good? Then you should take a closer look at the TIG welding process. In this article, you will learn everything that is important in a compact way.
What is TIG welding?
TIG welding is the abbreviation for tungsten inert gas welding. This is welding with a shielding gas. The process technology belongs to the group of fusion welding processes. It is particularly popular due to the fact that it enables particularly clean processing. Seams that have been processed using TIG welding are spatter-free and are generally of exceptionally good quality.
The TIG welding process is particularly flexible in the field of metal processing. Whether stainless steels, aluminum, nickel or even titanium, an almost endless range of materials can be used. The method also appears to be ideal for sheet metal made from an aluminum-stainless steel alloy. Examples of applications for TIG welding can be found in the aerospace industry and in the construction of containers, pipelines and pipelines.
How does TIG welding work?
In the TIG welding process, a welding arc is created between the tungsten electrode and the component. The shielding gas is usually an inert gas such as argon or helium. It prevents both the liquid weld seam and the electrode in the welding torch from becoming enriched with oxygen.
Although filler material is not absolutely necessary, it can be added if desired. In the case of TIG welding, it must be introduced directly into the liquid weld seam. In this respect, handling differs fundamentally from processing with the MIG/MAG welding torch.
Interesting facts about the tungsten electrode
Tungsten has the highest melting point of all pure metals. This successfully prevents the electrode from melting during the welding process. Tungsten electrodes are manufactured using the sintering process. An alloy with oxidic additives is also possible. The purpose of this is to optimize the electrode properties, such as current carrying capacity or ignitability. Differentiation is achieved by using different colors for each alloy.
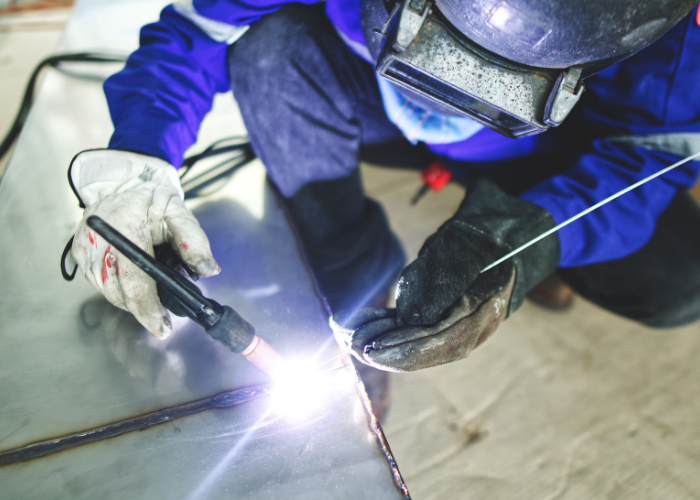
What process variants of TIG welding are there?
Various types are available depending on the material and target. Their summarized description is given below.
Cold wire welding
During cold wire welding, the optional filler material is added precisely and evenly to the liquid bath. This method is best suited to those who are still new to TIG welding and also increases productivity.
Hot wire welding
When we talk about hot wire welding, this means that the filler material is additionally heated. The aim is to increase the deposition rate and the deposition capacity. At the same time, the process ensures a higher welding speed and a reduction in mixing. The origin of the idea of hot wire welding comes from its big brother, cold wire welding.
Orbital welding
In orbital welding, the welding tool rotates 180 or 360 degrees around the fixed workpiece. CNC control is used here, which requires only minimal intervention on the part of the welder. This makes the method safer than manual handling and limits possible human application errors. In addition to joining two pipes, orbital welding is particularly suitable for welding pipes to the tube sheet.
ArcTig
The ArcTig process is a mechanized method of joining two workpieces by welding. The procedure guarantees reliable welding at the root and is characterized by high speed. Due to the speed and the fact that the preparation of the weld seam is limited, the ArcTig welding process can generally be described as very economical.
Cladding
In cladding, the workpieces to be processed are given a special alloy through mechanized build-up welding. The purpose of this is to extend the service life.
What makes TIG welding special?
Unlike other welding processes, TIG welding is not just about the pure joining action of components, but in particular about the appearance of the finished workpiece. A clean weld seam is always the goal, which requires particularly precise handling during the entire welding process.
A lot is required of the welder himself: He must be able to push the welding torch forward with one hand, while adding any filler materials very carefully and slowly to the molten weld pool with the other hand. Unlike with the MIG/MAG welding torch, the welder cannot additionally support the TIG welding torch, which requires special expertise and dexterity.
The result makes the TIG welding method the number one choice when it comes to high-quality processing. At the same time, TIG welding is probably one of the most demanding types of joining. The trial and error principle can be expensive, which is why many companies prefer to outsource their production to experienced service providers in this field.
The advantages of TIG welding at a glance
- 1A welding quality
- Visually perfect weld seams
- No welding spatter
- All welding positions possible
Get a quote for your parts
Conclusion – We offer optimal support
TIG welding is particularly beneficial for companies that expect not only durable products but also visual perfection. Hardly any other process offers such high-quality weld seam processing. In addition, TIG welding technology is extremely versatile in use and a wide range of base materials can be used.
We at CNC24 are also flexible. As a professional digital manufacturer 4.0, we offer all modern CNC production processes. We also focus on excellent service and offer special services, such as the production of complex precision components. With over 500 hand-selected producers from Europe and all over the world, we can deliver what you need in no time at all – and if you need it fast, we can also provide express production up to 72 hours after receipt of order.
Curious? Then get in touch with us today. We will send you an offer tailored to your project within 48 hours.
Optimization of your supplier search
Download Whitepaper
Find out now which 9 points you should consider so that you can find the right supplier and reduce your costs by up to 40%.
Please note that the whitepaper is only available in the German language.
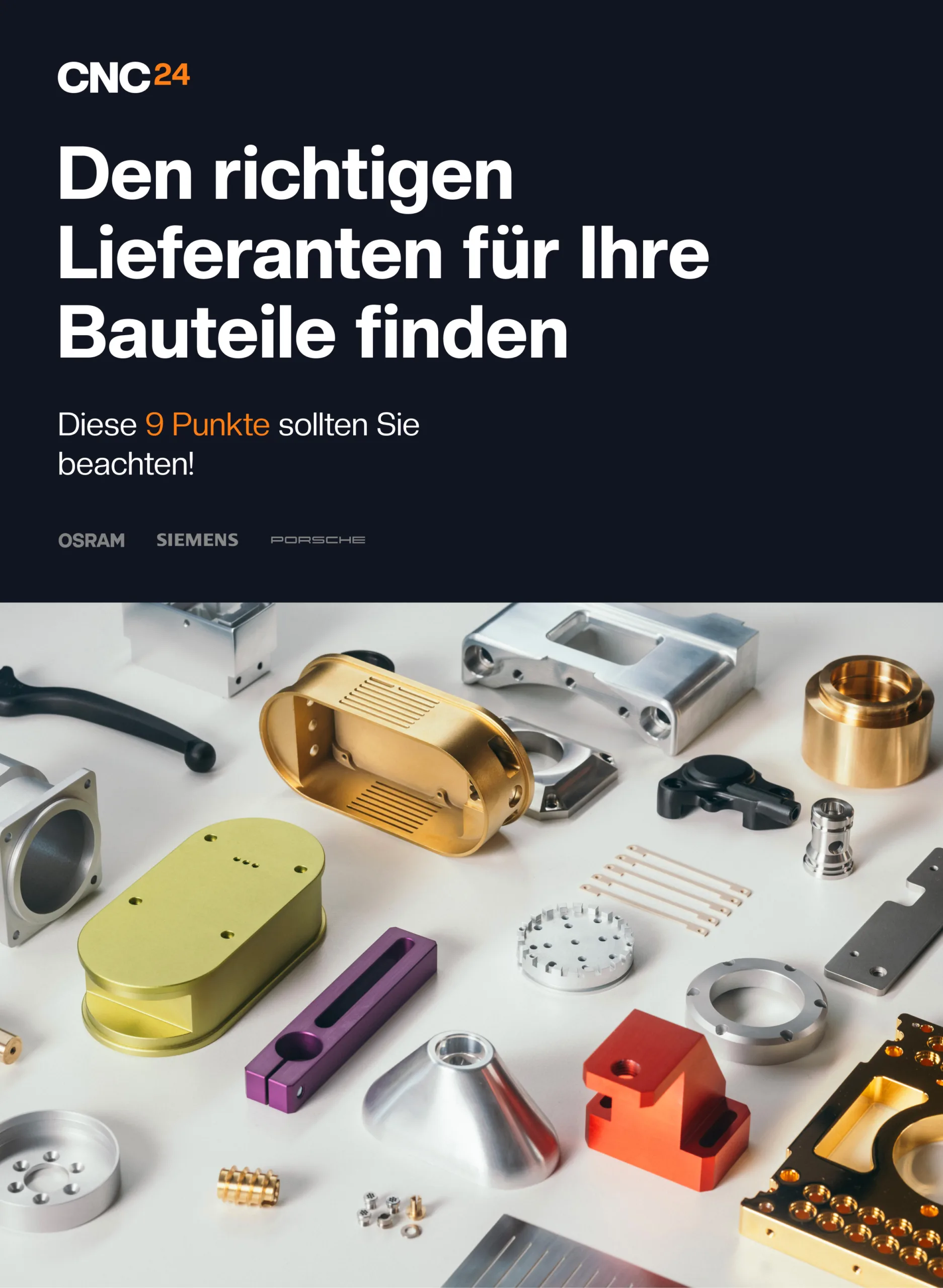