CNC turning and milling – which is better?
manufacturing process in the industry. With the help of modern computer technology and AI, the most complex shapes are created seemingly effortlessly from turned or milled parts.
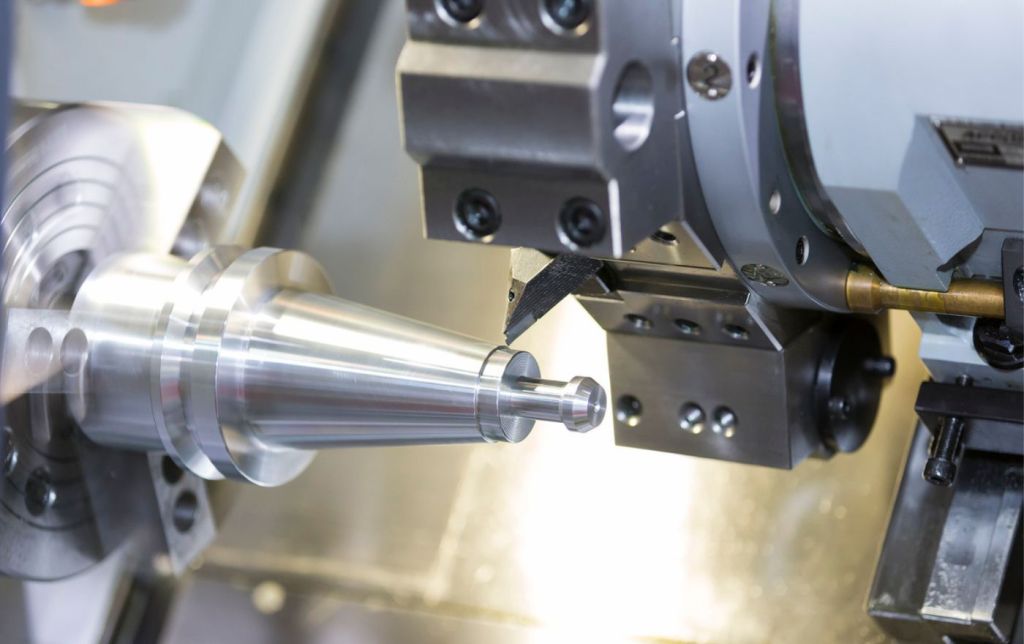
Both CNC turning and CNC milling are currently the most widely used manufacturing processes in the industry. With the help of modern computer technology and AI, the most complex shapes are created seemingly effortlessly from turned or milled parts.
What is CNC turning?
CNC, the abbreviation for “Computerized Numerical Control”, symbolizes computer-controlled precision control in manufacturing technology, especially applied to CNC turning. This method is mainly used for machining cylindrical or conical components.
CNC turning is the second most popular manufacturing method, right after CNC milling. In simple terms, the fixed component rotates while a turning tool approaches it to remove material layer by layer. The choice of the specific turning process depends mainly on the nature of the material and the surface of the workpiece. The most common techniques include
- Shape turning
- Facing
- Hob turning
- Round turning
- Profile turning
- Screw turning
What is CNC milling?
CNC milling, ideal for geometric components, uses advanced CAD programs for precise contour models. This process allows milling machines to remove material layer by layer to achieve the desired shape. CNC milling is valued for its speed and high quality.
Popular CNC milling processes include:
- CNC face milling
- CNC hobbing
- CNC screw milling
- CNC form milling
- CNC plunge milling
- CNC profile milling
CNC milling machines work with up to six axes, three of which are main axes and others are auxiliary axes. CNC24 uses 3-axis milling for simple tasks and 5-axis milling for complex geometries. The performance of CNC milling machines remains impressive.
What is the difference between turning and milling?
The main difference between CNC turning and CNC milling is the way in which the material is processed. During the turning process, the workpiece being machined rotates in order to be shaped. In contrast, during milling, the workpiece remains stationary and only the tools move.
The choice between turning and milling depends on various criteria:
Cut type
- In CNC milling, the contact is intermittent due to the varying engagement of the milling teeth
- There is continuous contact with the workpiece during turning
Shape and geometry
- Turning is more suitable for cylindrical or conical shapes
- Milling is ideal for flat surfaces or irregular sheet metal.
Costs
- Turning is more cost-efficient, but limited to simpler shapes
- Milling allows more versatile cuts and is suitable for more complex requirements
Tools and cutting processes
- Lathes usually use a single cutting tool and produce both continuous and discontinuous chips.
- Milling machines use several cutting tools and only produce discontinuous chips.
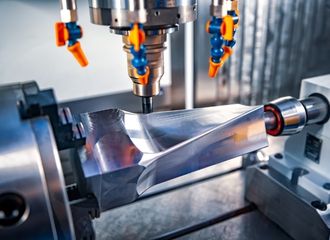
Which technology is suitable for which areas of application?
To make the decision between turning and milling a little easier for you, it also helps to look at both types of process again in detail and then compare them with your desired result.
CNC turning
CNC turning is particularly suitable for round surfaces. With the necessary expertise of the milling cutter, a precise and attractive finish can be achieved. The excellent backward compatibility and the possibility of creating asymmetrical shapes speak in favor of the turning process when choosing between CNC turning and milling.
Some products that are particularly suitable for production using CNC turning are:
- Nuts and screws
- Gear wheels
- Rollers
- Housing
- Tubes
- Slices
- Bar
- Burner nozzles
- Ball joints
- Turbines
You can CNC turn almost all machinable materials. Popular in this context are
- Aluminum
- Bronze
- Steel
- Stainless steel
- Hard fabric
- Inconel
- Ceramics
- Brass
- Titanium
- Copper
CNC milling
When it comes to complex shapes, custom-made products or series production, the extra cost of CNC milling is justified. This technology is also ideal for creating holes, recesses or consolidations in workpieces.
As already mentioned, there are hardly any restrictions when it comes to the choice of materials for turning and milling. The most frequently requested materials for milling at CNC24 include:
- Aluminum
- Ceramics
- Bronze
- Plastics
- Steel
- Brass
- Casting
- Titanium
- Hard fabric
- Stainless steel
- Copper
Which is better CNC milling or CNC turning?
The advantages in comparison
- Realization of complex shapes, custom-made products
- Ideal for holes, recesses
- Precise end result, high quality
- Fast production, reduced set-up times
- Safety and low error rate thanks to computer control
- Suitable for series productions
- Fast production of simple molds
- Precise and high quality
- Short set-up times, predictable production times
- High safety standard, minimal error rate
- Cost-efficient
Get a quote for your parts
About CNC24
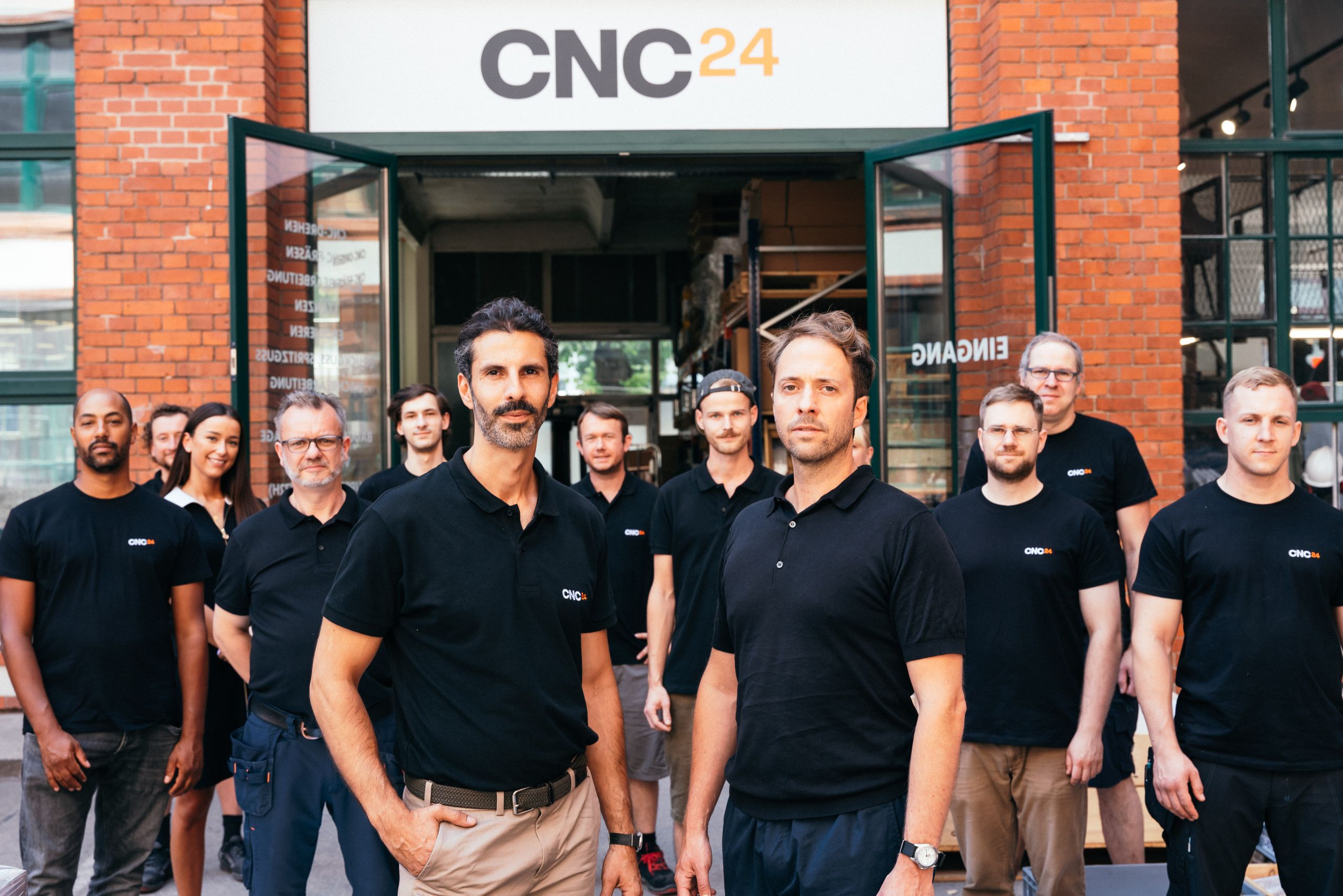
CNC24, a brand of CNC24 GmbH, is a digital B2B procurement platform through which individual precision components can be sourced transparently and efficiently. Manufacturers from 22 countries produce the mechanical components individually according to customer specifications. The manufacturing processes offered by the leading online marketplace for mechanical engineering include turning, milling, sheet metal processing and additive manufacturing.
With its innovative platform solution, the technology company creates a transparent process for the procurement of production parts and digitalizes the value chain through to a fully automated procurement process.
The company’s successful positioning as a partner for SMEs in the field of digitalization and innovation was confirmed in 2023 when it was awarded the German Excellence Award in the “Digital Startup Champions” category and the “Employer of the Future” seal. Thanks to its global network of suppliers, the company can guarantee free capacity, high material availability and on-time delivery of components at all times.
For quality control, all parts undergo an additional inspection process in the in-house measuring center before they are delivered. CNC24 was founded in 2019 by co-founders Willi Ruopp and Marlon Gerat. The start-up serves all industrial sectors with a need for production parts – from special machinery and plant engineering to IOT and medical, testing and measurement technology.
In summary, both processes deliver high quality and speed. CNC milling is ideal for more complex shapes and custom-made products, while turning is efficient for simple shapes in large quantities, with fast series production at an excellent price.
CNC24 will be happy to advise you on the decision between turning and milling your components.
Optimization of your supplier search
Download Whitepaper
Find out now which 9 points you should consider so that you can find the right supplier and reduce your costs by up to 40%.
Please note that the whitepaper is only available in the German language.
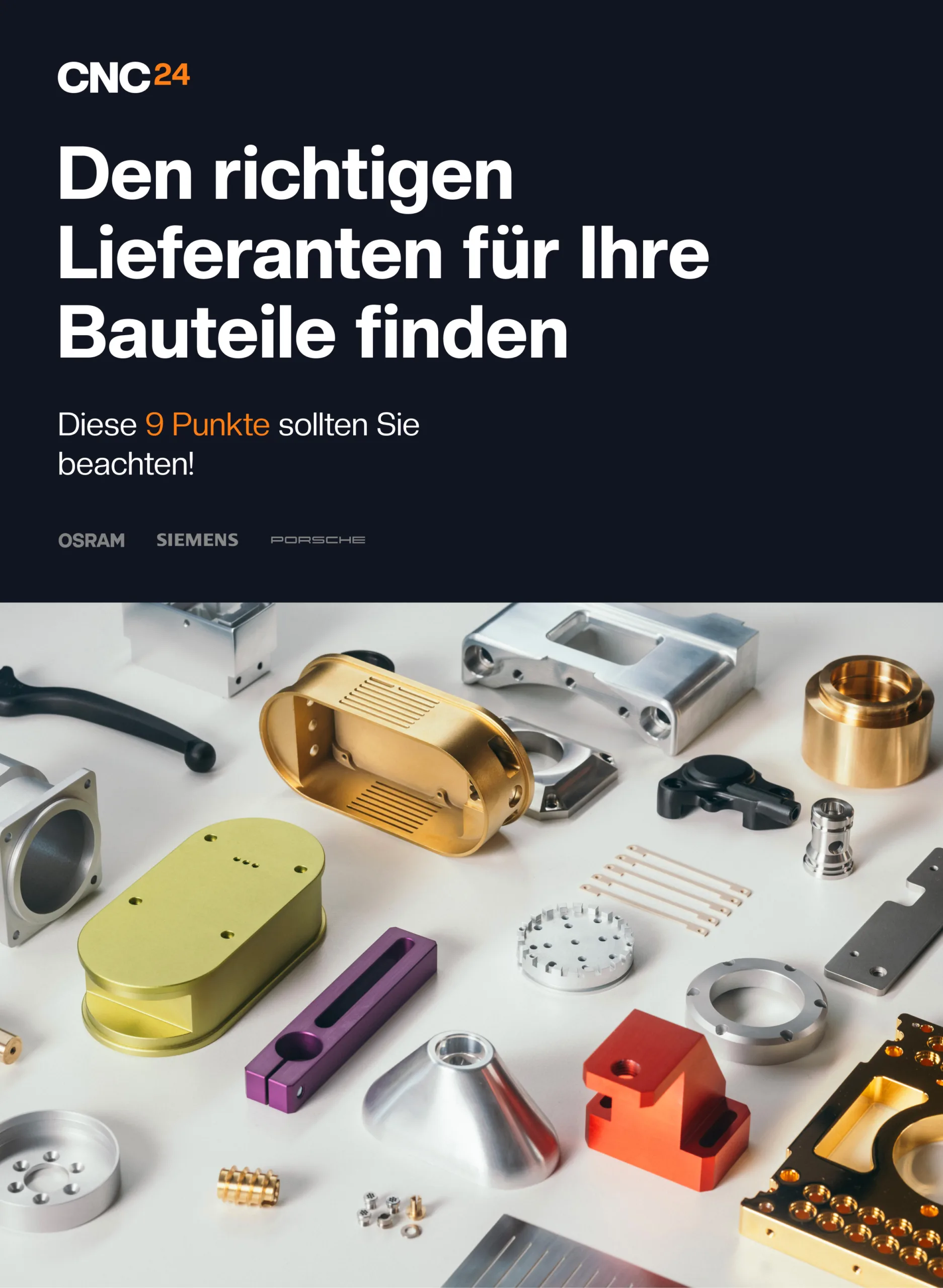