Punching sheet metal – how does it work?
In this article, you will learn more about punching sheet metal.
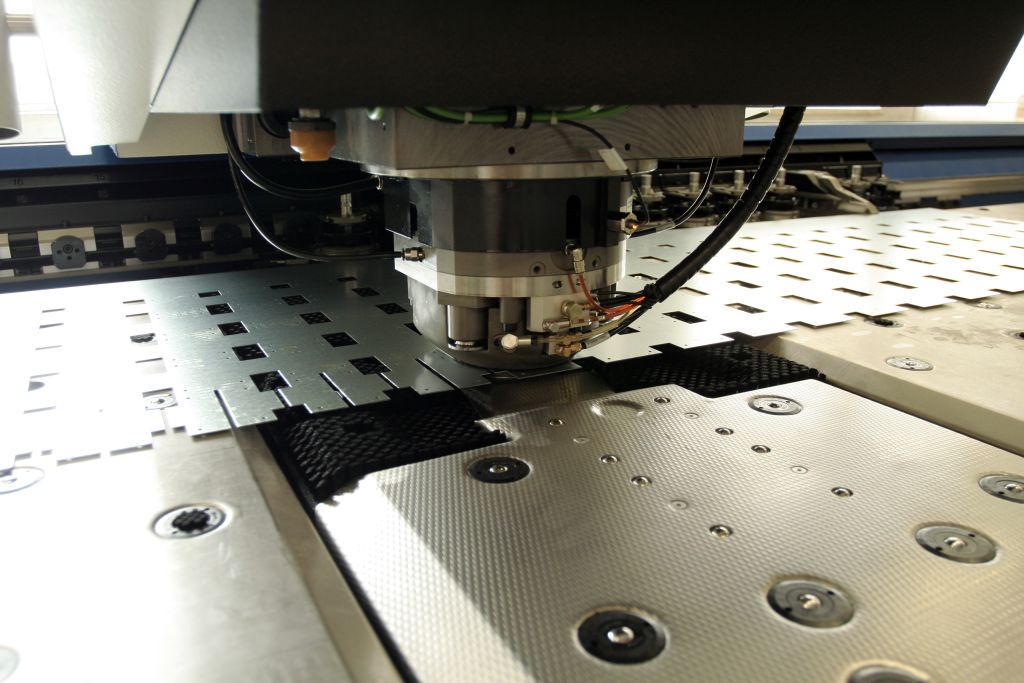
Punching sheet metal
Punching has always been one of the most popular separation and cutting processes, and for good reason. With one particular feature, it often even beats laser cutting in the rankings.
In this article, you will learn more about the topic of punching sheet metal. You will receive valuable information about the types as well as the advantages and disadvantages of the processing method. You will also find out in which cases it makes sense to outsource sheet metal work
Do you want to make a large number of deformations, perforations or openings in sheet metal? Then punching is the preferred method. Compared to various other processing methods, this processing method also offers particular advantages.
Precision
Modern punching tools have excellent precision and dimensional accuracy when working. This means that identical and accurately fitting sheet metal parts can be produced quickly in series using this process. You can also rely on consistent quality.
Diversity
The punching process offers you a wide range of different shaping options. As already mentioned at the beginning, punching is generally the first choice for forming and drilling in particular. Many companies prefer to opt for this type of processing, especially when producing recesses, beads, gills and threads.
Simplicity
Punching is a mechanical processing method. This means that the preparation of the sheet metal parts does not take an excessive amount of time. It does not have to be melted or undergo any other thermal process. Although it is also of the highest standard, this is the case with laser cutting of sheet metal, for example.
Not sure whether you should punch or laser cut your components? Why not do both! At CNC24, we also have combined punching and laser systems. We will be happy to advise you.
Cost and energy efficiency
Modern machining centers rely on automated punching with CNC sheet metal processing technology. So do we at CNC24. This modern process not only saves you an enormous amount of time, but can also significantly reduce manufacturing costs. As there is no need for any thermal processing, the production of sheet metal parts during punching is also energy-saving.
Sheet metal punching – The biggest advantages at a glance
- Cost-effective and energy-saving process
- Precise cut-outs, openings and embossing possible
- Clear recommendation for series production
- Mechanical production without thermal deformation
- High throughput times with consistently high quality
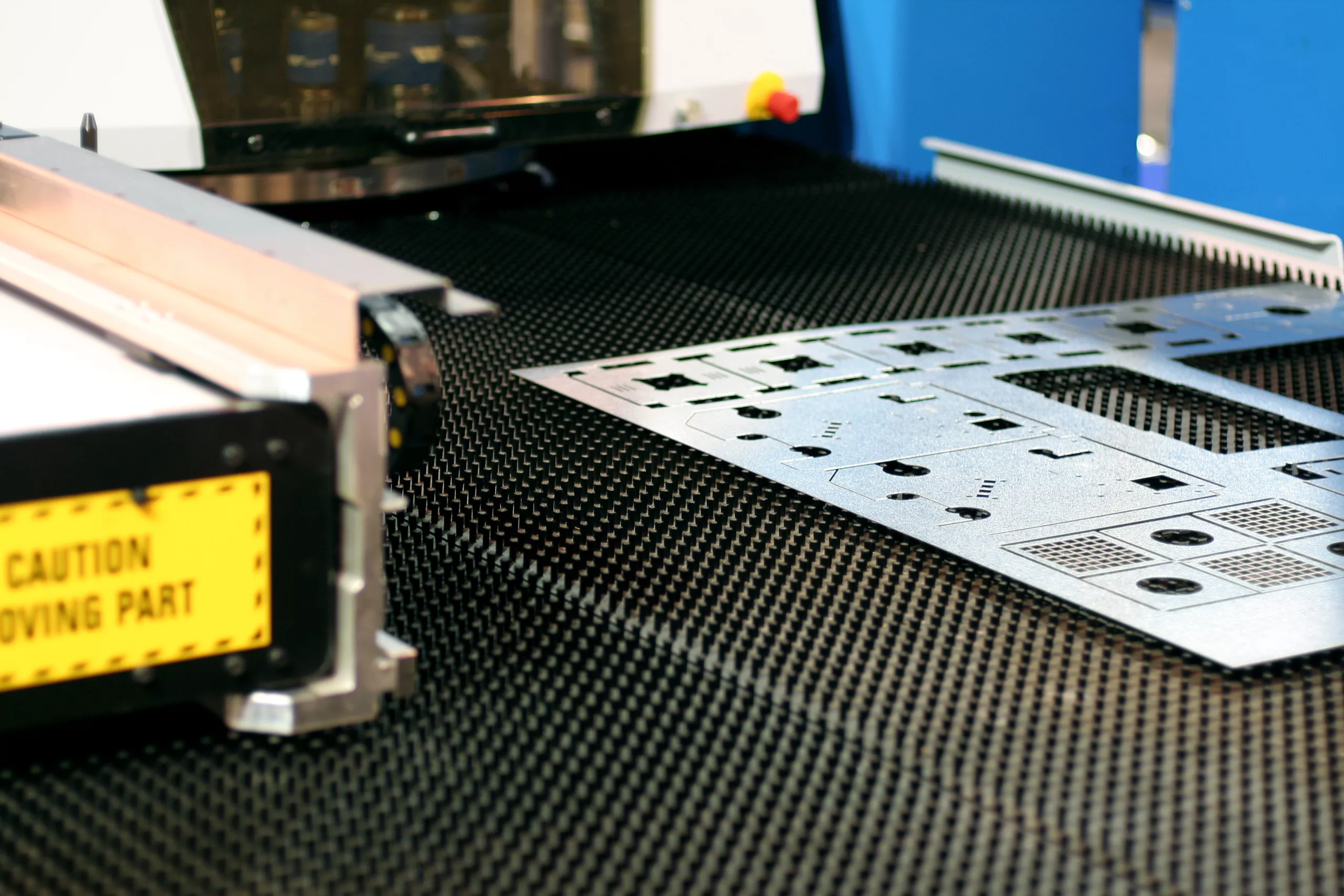
What sheet metal punching techniques are there?
Punching refers to the processing of various materials, especially metal, which are usually supplied in sheet form. In addition to the metalworking industry, the paper, textile, plastics and paper industries also use this process. There are various process technologies for punching sheet metal. Modern punching machines can do much more than just punching. They are multi-tools that can be used for various processing steps.
The following are among the common processing techniques used in sheet metal punching:
- Cutting
Wedge or shear cutting is usually used for this cutting method. - Forming
One of the biggest advantages of punching machines in contrast to laser technology is that they can also form, for example by using bending tools. - Joining
Joining is the process of bringing two workpieces together. This is done, for example, by riveting, pressing or folding.
Get a quote for your parts
And what is shear cutting?
Shear cutting refers to the cutting processes used in punching. These can also be divided into their own categories. These are
- Cutting out
This is done in the case of a shape with a closed cutting line. - Cutting off
This refers to classic cutting at the cutting line. - Punching
If a hole is punched in the sheet, the closed cutting line is clearly visible. - Notching
This refers to the cutting out of areas along the edge. - Incision
The word is often used in preparation for bending or drawing work. This causes a partial separation of the material. - Trimming
This process is used, among other things, to separate edges. - Trimming
During trimming, excess material is removed from the material. - Cut-off cutting
Several sheet metal parts can be processed from a specific initial shape. - Re-cutting
This is the finishing technique after punching sheet metal. The edges are reworked and cut off if necessary. - Nibbling
What sounds fun actually means the gradual removal of material particles.
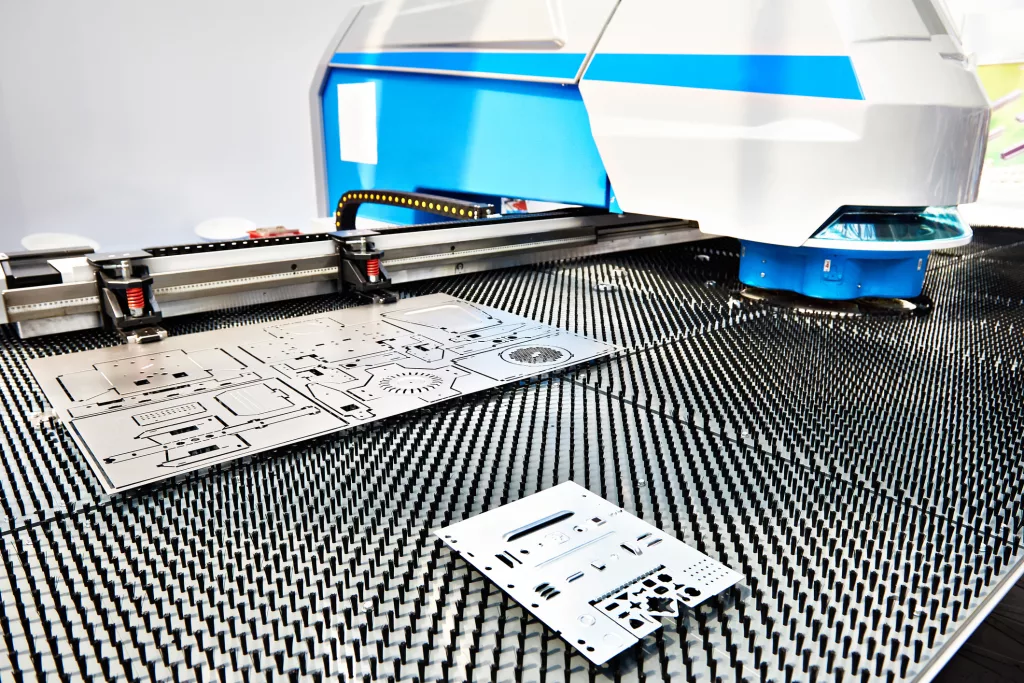
Disadvantages of sheet metal punching – why you should rely on experts
Where there are many advantages, there are also disadvantages. These crystallize when punching:
High acquisition costs
Punching tools are anything but cheap. If you want to punch yourself, we recommend purchasing a professional punching machine for series production; for smaller-scale projects, it makes sense to outsource this work to experts such as CNC24.
Limited flexibility
Punching is for larger projects in series. The same applies to the size of the desired shapes in sheet metal. The smaller, the more difficult it is. The size of a hole in sheet metal depends roughly on the thickness of the sheet metal: a sheet metal with a certain diameter cannot have a larger diameter hole.
Beispiel: Blechdicke 4 cm = Loch minimal 4 cm
Laser cutting is the alternative of choice here.
Post-processing necessary
If you have older punching tools, you will have heard that a punching burr forms during punching. This is then located under the sheet metal and needs to be removed for an optimum result. Modern machining centers have a solution for this: they often have appropriate deburring tools that ensure fast removal and maintain high edge quality.
Nibble marks
Nibble marks are typical when punching sheet metal if the punching tool is offset after the stroke for the longest possible cut. If these nibble marks are not to be visible, they must be removed. The multishear tool is the ultimate weapon in professional sheet metal punching: it can be used to verify perfect cut edges.
Get a quote for your parts
Conclusion: How CNC24 can support you with sheet metal punching
The punching process has a long tradition. And even at a time when ultra-modern manufacturing processes with laser technology amaze us, punching and nibbling are still often the immediate choice for perforations, embossing and other forming requirements in sheet metal.
Modern punching is without doubt a high-precision process with which we can realize your wishes quickly and in a cost- and energy-efficient manner.
Our team at CNC24 can punch sheet metal and sheet metal products for you with little to no scratches, depending on the punching process. We can proudly say that we have hundreds of punching tools and stand combination tools with which we can implement your wishes quickly and at an attractive price.
Sounds interesting?
Then get your non-binding quote today – you will receive it within 48 hours. You can find more information on other sheet metal processing services here.
Sheet metal punching with CNC24 – Technical data
Material thickness: | up to 8 mm |
Diameter: | max. 30 mm |
Geometries: | round, square, rectangular |
Ideal batch size: | from 2,000 pieces |
Our choice of materials
- Aluminum
- Copper
- Brass
- Bronze
- Stainless steel
- Steel
- Spring steel
Optimization of your supplier search
Download Whitepaper
Find out now which 9 points you should consider so that you can find the right supplier and reduce your costs by up to 40%.
Please note that the whitepaper is only available in the German language.
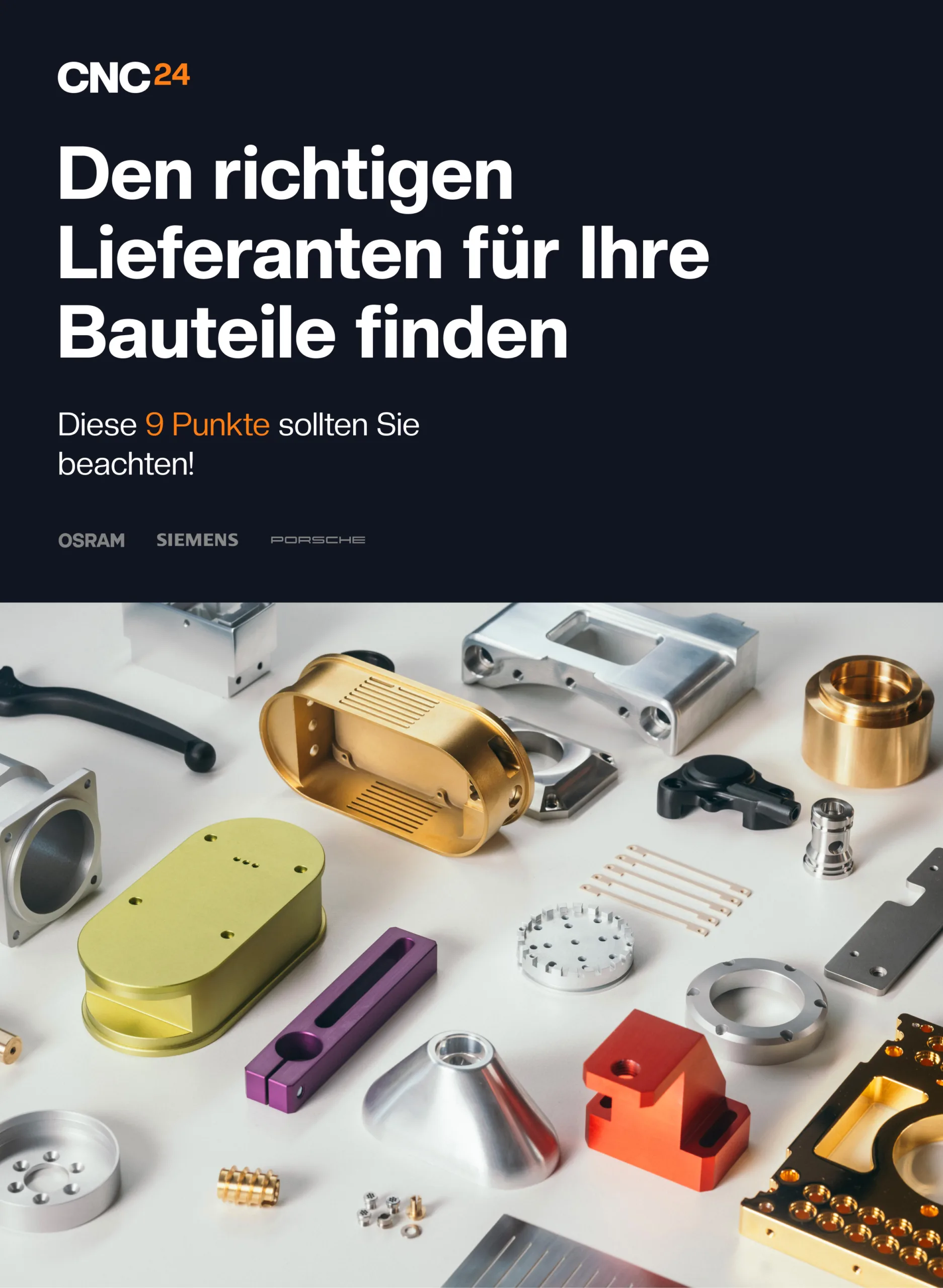