Production of pressed parts: Guide to manufacturer selection
Find out everything you need to know about the production of pressed parts and what is important when choosing the right manufacturer in our guide.
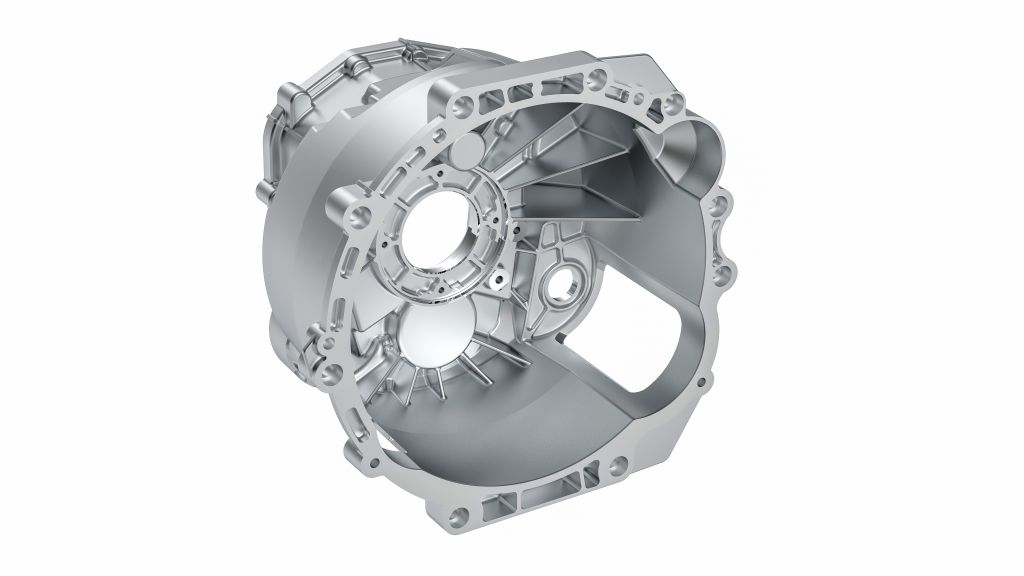
Are you a purchasing manager looking for high-quality pressed parts for your projects?
In this guide, we provide you with detailed information on what is important when selecting manufacturers for pressed parts and which criteria you must take into account when choosing a manufacturer.
Advantages and disadvantages in the production of pressed parts
The production of pressed parts offers a number of advantages and disadvantages.
The advantages include high production speed, precise shaping and the ability to produce complex geometries. In addition, large quantities can be produced cost-effectively, which supports mass production.
However, setting up and maintaining presses often requires considerable investment. In addition, high tooling costs and long set-up times can be a challenge, especially when producing smaller quantities or with frequent product changes. Finally, the forming of pressed parts can lead to material losses and limit flexibility in adapting to design changes.
Advantages
- Pressed parts offer high dimensional accuracy, which is essential for many technical applications.
- Mass production of pressed parts can significantly reduce unit costs.
- The production of pressed parts enables efficient material utilization and reduces waste.
- Modern pressing processes enable fast production and therefore short delivery times.
- By using different materials and alloys, pressed parts can be produced for special requirements.
Disadvantages
- The initial investment for pressing tools and machines can be very high.
- Converting or adapting pressing tools in the event of changes can be costly and time-consuming.
- The production costs per pressed part are higher for small quantities.
- The quality of the pressed parts depends heavily on the precision of the tools and the experience of the operating personnel.
- Special materials and alloys can increase the production costs of pressed parts.
ISO certification as a quality feature for manufacturers
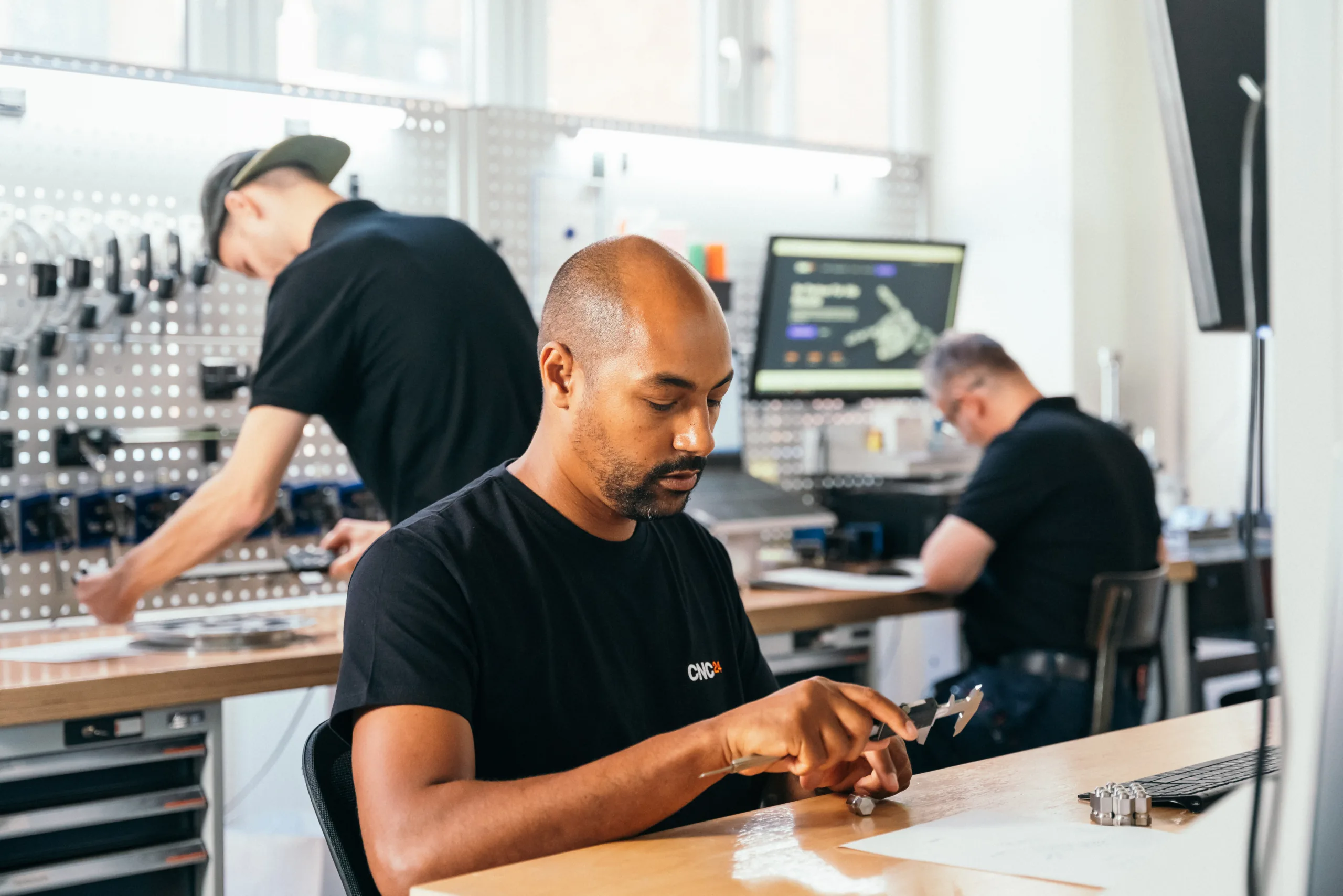
When selecting manufacturers, there are certain quality criteria that you should definitely consider in your selection process.
ISO 9001 certification is particularly worthy of mention here. ISO 9001-certified manufacturers offer a number of advantages for their customers. First of all, ISO 9001 certification indicates that the manufacturer has introduced a quality management system that meets internationally recognized standards. This increases the reliability and consistency of products as processes are systematically monitored and improved.
As a customer, you can also rely on the fact that ISO 9001-certified manufacturers produce their products in accordance with defined quality standards and that these standards are regularly checked and updated.
Further selection criteria for manufacturers of pressed parts
In addition to ISO certification, criteria such as experience, precision and reliability are of crucial importance in the production of pressed parts.
The manufacturer should be experienced in working with different materials such as steel or aluminum and also have the appropriate technical equipment.
If you also include these points in your selection process, you can expect to obtain components of outstanding quality.
Cost factors in the procurement of pressed parts
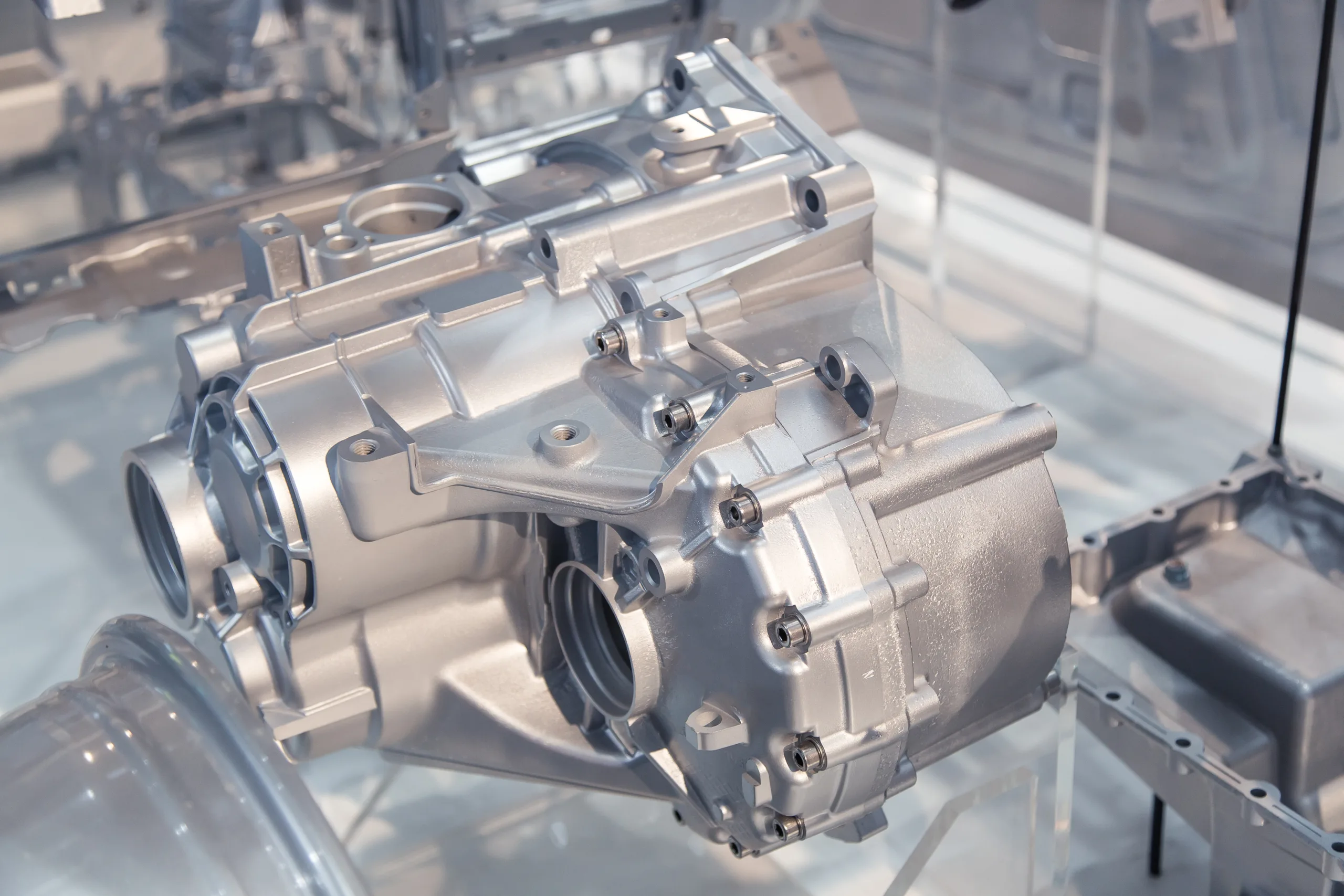
When procuring pressed parts, the costs essentially depend on the material. As each raw material has specific properties, the material selected also has a direct impact on the production costs.
Steel, for example, is very robust and cost-efficient to process, while aluminum is lighter but more expensive to manufacture.
It is therefore always worth obtaining quotes from different manufacturers in order to compare prices. Factors such as delivery times, quality assurance and downstream services should not be ignored.
In addition, always try to establish a long-term partnership with the manufacturer, as this can lead to lower prices or better conditions for recurring orders.
Get a quote for your parts
Conclusion
The manufacturer of pressed parts should by no means be chosen lightly.
Make sure that the manufacturer exactly matches your needs in all the aspects described above.
This is the only way to ensure that you receive components of the quality you require.
Top tips for buyers of pressed parts
- ISO 9001 certification should always serve as a basis for cooperation.
- Make sure that the manufacturer has a reliable supply chain.
- Clarify the manufacturer’s production capacities.
- Arrange a tour of the production facility before starting a collaboration.
EXTRA: A quick guide to shape and position tolerance symbols
About CNC24
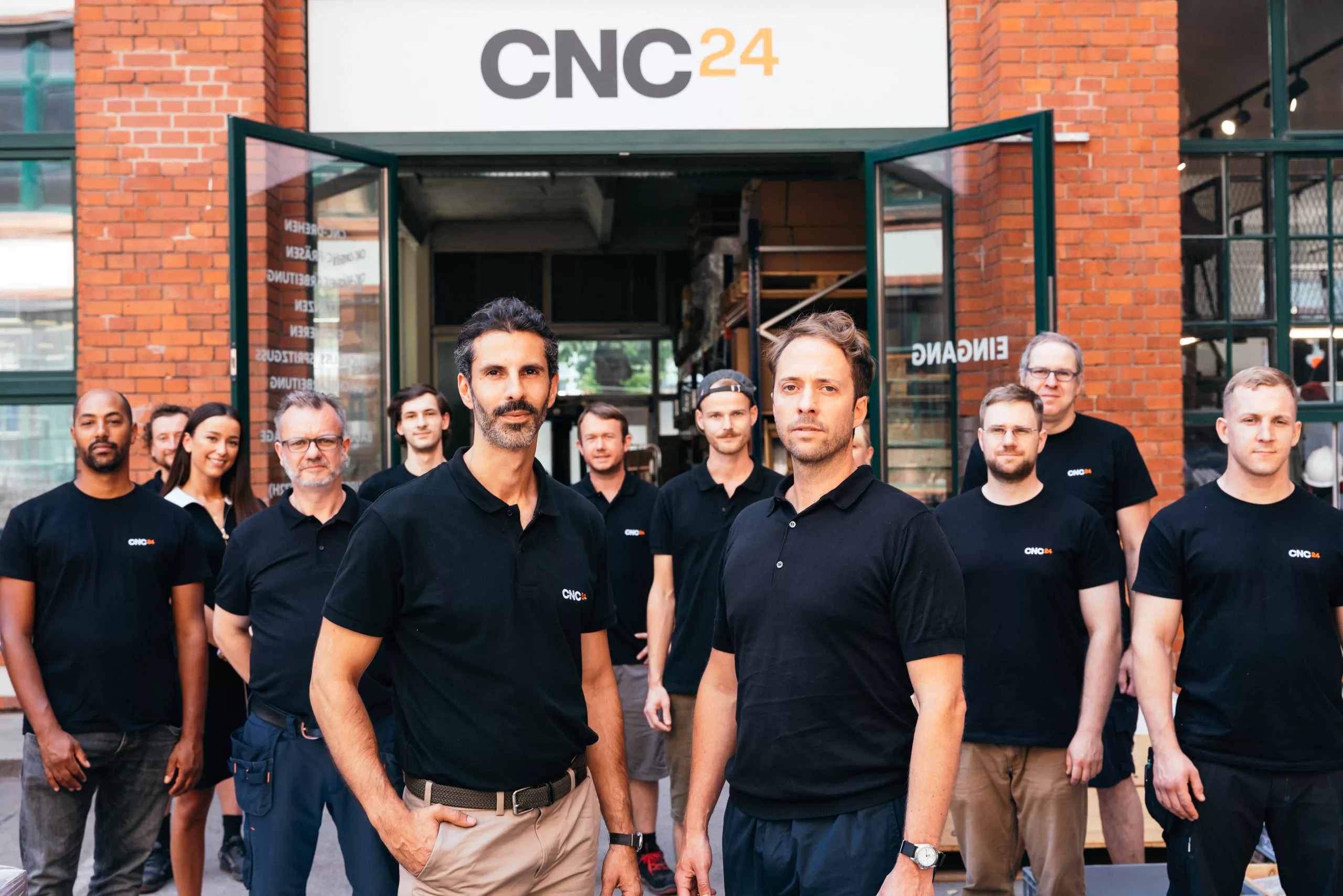
CNC24, a brand of CNC24 GmbH, is a digital B2B procurement platform through which individual precision components can be sourced transparently and efficiently. Manufacturers from 22 countries produce the mechanical components individually according to customer specifications. The manufacturing processes offered by the leading online marketplace for mechanical engineering include turning, milling, sheet metal processing and additive manufacturing.
With its innovative platform solution, the technology company creates a transparent process for the procurement of production parts and digitalizes the value chain through to a fully automated procurement process.
The company’s successful positioning as a partner for SMEs in the field of digitalization and innovation was confirmed in 2023 by the award of the German Excellence Prize in the “Digital Startup Champions” category and the “Employer of the Future” seal.
Thanks to its global network of suppliers, the company can guarantee free capacity, high material availability and on-time delivery of components at all times.
For quality control, all parts undergo an additional inspection process in the in-house measuring center before they are delivered. CNC24 was founded in 2019 by co-founders Willi Ruopp and Marlon Gerat. The start-up serves all industrial sectors with a need for production parts – from special machinery and plant engineering to IOT and medical, testing and measurement technology.
Survey on the Status of Component Procurement
Download Industry Paper
We have structured the most important findings for you and presented them clearly in an industry paper.
Please note that the survey is only available in the German language.
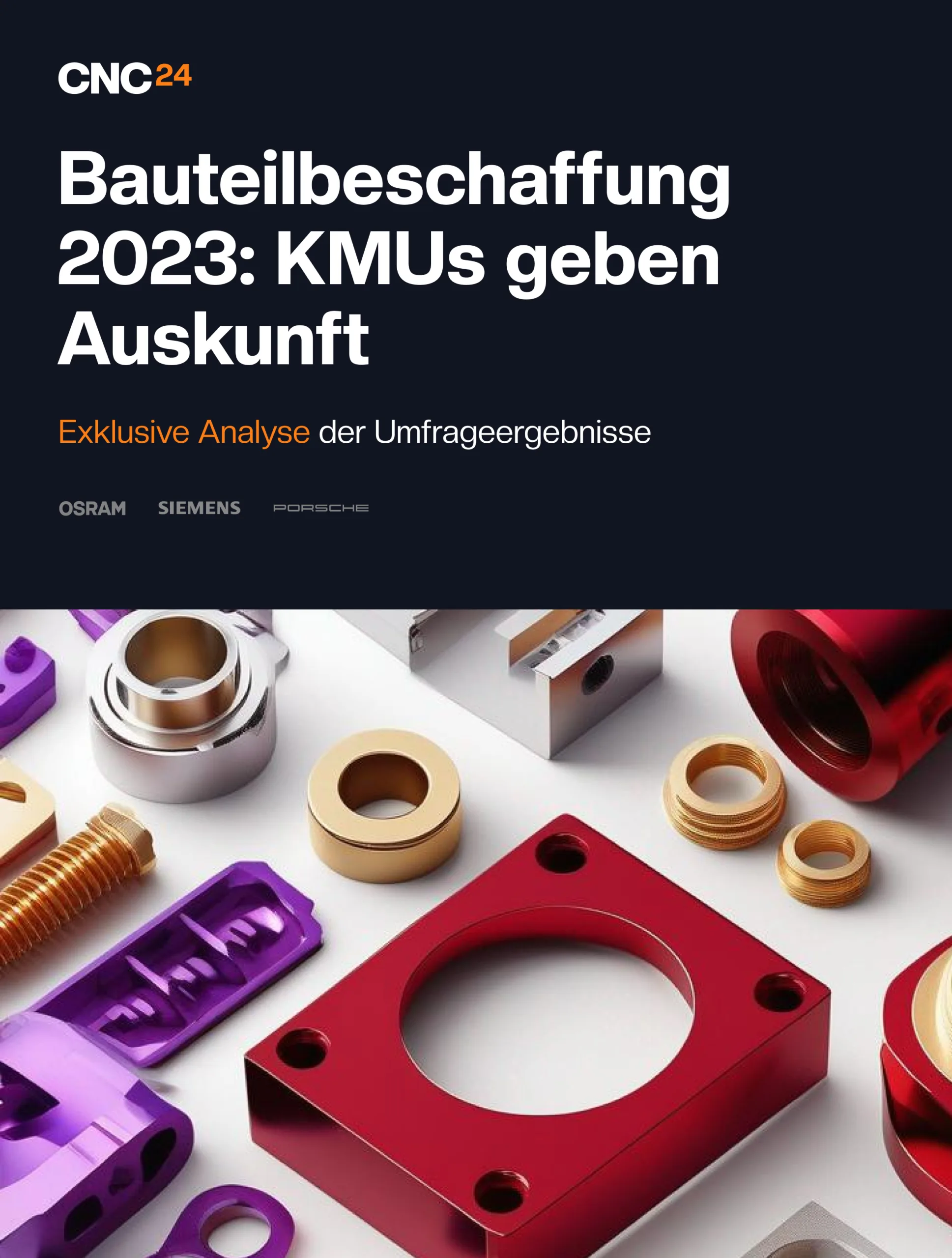