Laser cutting vs. waterjet cutting: A detailed comparison
Find out more about techniques, costs and which method is best suited for which material.
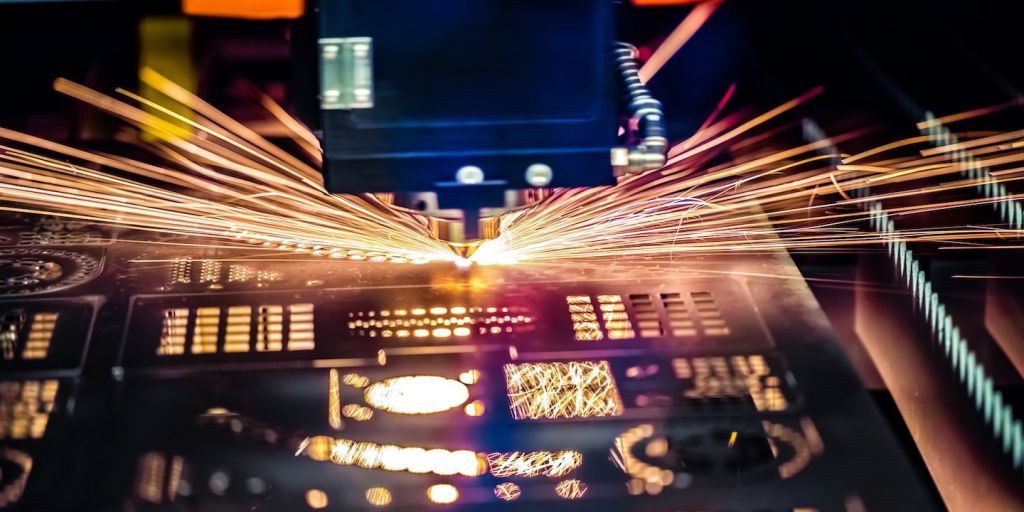
In the field of industrial cutting, the debate between laser cutting and waterjet cutting is omnipresent. Both are valuable technologies that offer unique advantages and enable precise cuts. This article provides a comprehensive overview of their characteristics, efficiency and applications.
Type of processing:
- Laser cutting: Use of a high-intensity laser beam that heats and vaporizes the material.
- Waterjet cutting: Uses a high-pressure jet of water, sometimes mixed with abrasive substances, to remove the material. Laser and waterjet cutting
Versatility of the material:
- Laser cutting: Efficient with metals such as steel, aluminum and others. Problems can occur with thicker materials and reflective metals.
- Waterjet cutting: Suitable for almost all materials, including metals, plastics, glass and even rubber. No heat-affected zones mean no material deformation.
Precision and surface quality:
- Laser cutting: Enables extremely precise cuts with a smooth surface. The accuracy can be up to 0.1 mm.
- Waterjet cutting: Although accurate, the surface may require secondary processes to make it smooth. Typically achieves an accuracy of 0.2 mm. Precision cutting.
Safety and environmental compatibility:
- Laser cutting: Generates vapors that need to be extracted. The process is relatively quiet.
- Water jet cutting: Does not produce hazardous waste, but can be noisier due to the high-pressure water jet.
Speed and efficiency:
- Laser cutting: Faster with thin materials, but can be slower with thicker materials.
- Waterjet cutting: The speed is constant, but generally slower than with laser cutting.
Impact on costs:
- Laser cutting: Uses more energy, but has no consumables such as abrasives, so operating costs can be lower.
- Waterjet cutting: Higher operating costs due to higher abrasive consumption, but lower energy consumption.
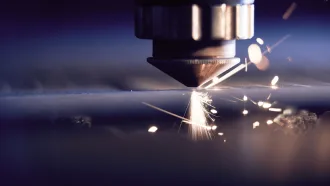
Laser cutting advantages VS waterjet cutting advantages
Advantages of laser cutting | Advantages of waterjet cutting |
Precision: Ideal for complex designs and patterns. | Versatility: Can cut practically any material. |
Speed: Faster cutting times for thin materials. | No heat: Eliminates thermal stress and potential warping. |
Clean cuts: Minimal debris or burr formation. | Environmentally friendly: No harmful vapors or gases are produced. |
- Precision: Ideal for complex designs and patterns.
- Speed: Shorter cutting times for thin materials. Clean cuts: Minimal waste and burr formation. Advantages of waterjet cutting
- Versatility: Virtually any material can be cut. No heat: Eliminates thermal stress and possible deformation.
- Environmentally friendly: No harmful vapors or gases are produced.
Which cutting technique should I choose?
The choice between laser and waterjet cutting depends largely on the material, the thickness and the desired surface.
Laser cutting is preferable for metals and thin materials where precision is important. For a greater variety of materials and thicker cross-sections, however, waterjet cutting is the better choice.
Optical comparison: laser vs. water jet
mindmap root((Techniques)) Laser cutting Highest precision Fast with thin materials Heat generation Water jet cutting Material versatility No heat distortion Abrasive consumption
Get a quote for your parts
Conclusion
Finding your way in the field of industrial cutting can be a challenge. Each technology, whether laser cutting or waterjet cutting, has its own advantages that are tailored to specific requirements. At CNC24, our experts specialize in guiding you through these choices to ensure you get the best cutting solution tailored to your unique needs.
Whatever the requirements of your project, we are here to provide you with the expertise and insight you need to achieve optimal results.
Optimization of your supplier search
Download Whitepaper
Find out now which 9 points you should consider so that you can find the right supplier and reduce your costs by up to 40%.
Please note that the whitepaper is only available in the German language.
