MIG/MAG welding: What is it?
The MIG/MAG welding process is as popular as ever. One of the reasons for this is its speed and cost-effectiveness.
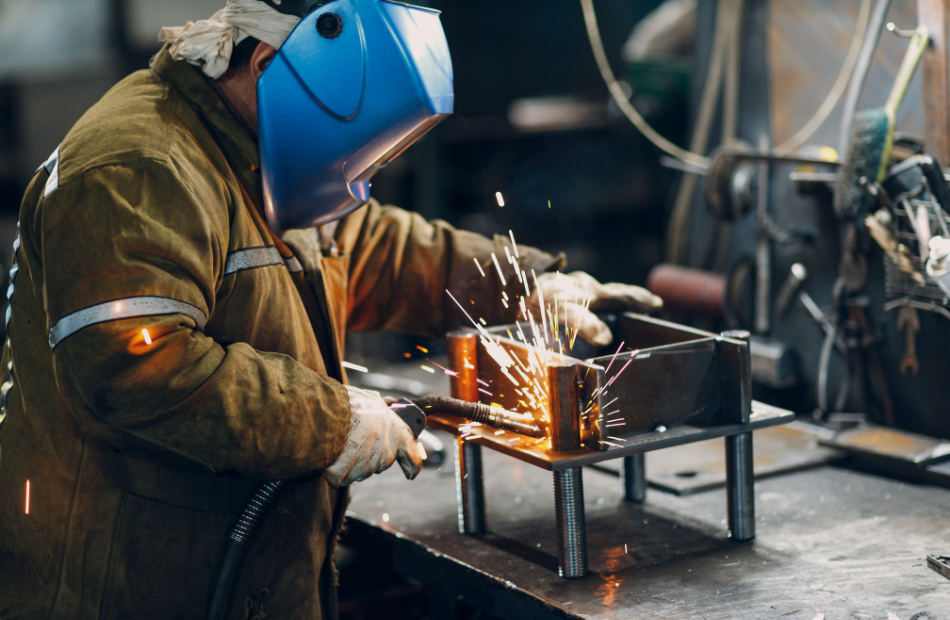
The MIG/MAG welding process is as popular as ever. One of the reasons for this is its speed and cost-effectiveness.
What is MIG/MAG welding?
MIG/MAG welding is the most widely used welding process today. It is also often referred to as gas metal arc welding.
The two abbreviations stand for metal inert gas welding (MIG) and metal active gas welding (MAG).
This already reveals the only difference between the two welding processes, which is simply the use of a different shielding gas.
MIG uses an inert gas, MAG uses an active gas. The inert gas does not react actively with the weld pool, whereas the active gas does.
The process technology of MIG and MAG is the same, although it can be carried out manually, mechanically or using computer-aided processes (e.g. welding robots). For this reason, MIG/MAG is usually referred to as one word.
A more detailed look at the differences between MIG and MAG
When MAG welding with active gases, a mixture of argon, carbon dioxide and oxygen is usually used. This prevents oxygen from penetrating the component to be welded and stabilizes the arc at the same time.
MIG welding with inactive gases is carried out with argon, helium or a mixture of both. As these gases do not react with the filler materials, a higher temperature can be calculated than with MAG welding and, under certain circumstances, even more time and money can be saved.
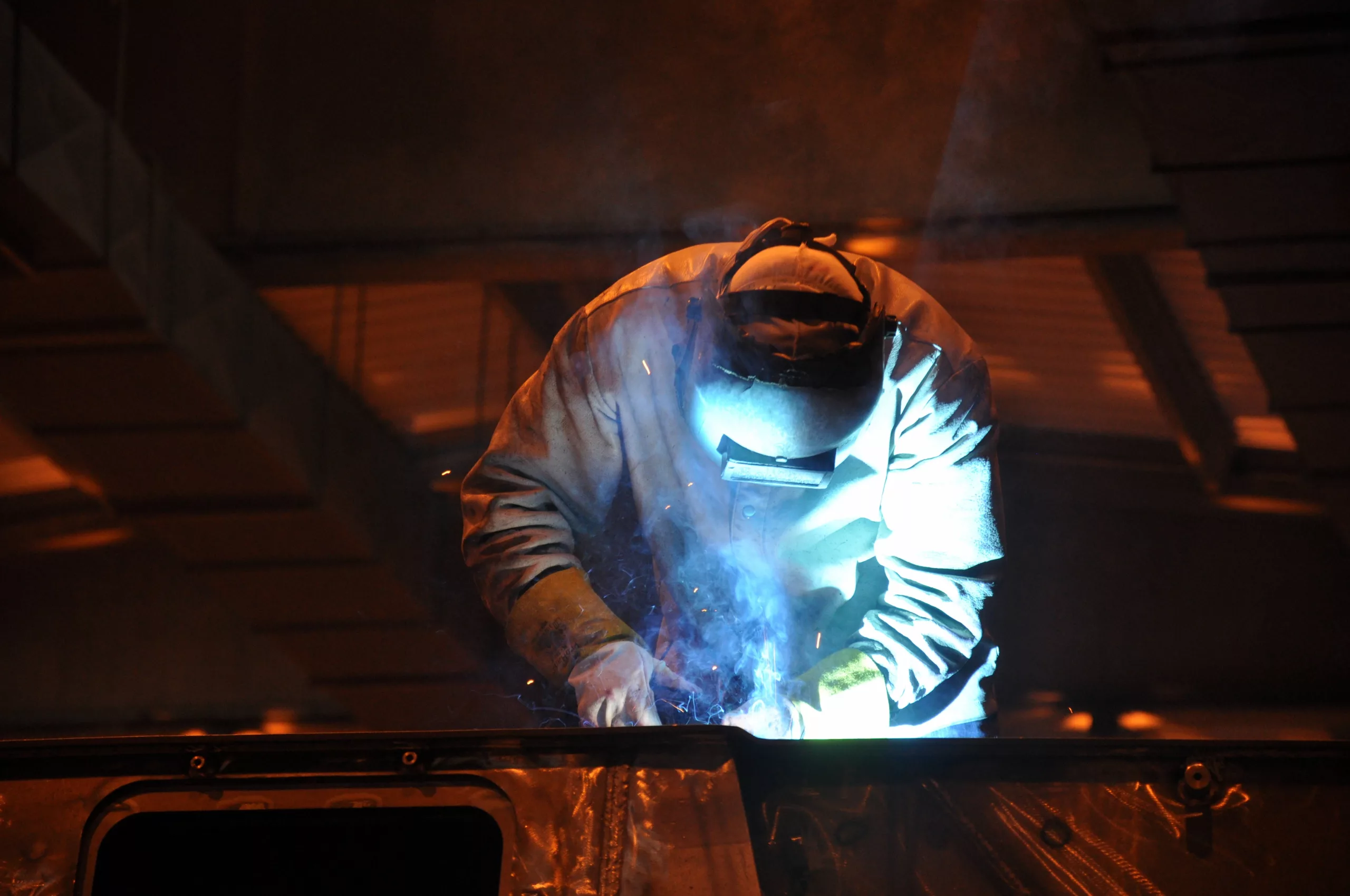
What is MIG/MAG welding used for?
- Reactive MAG welding is ideal for unalloyed and low-alloy steel as well as high-alloy materials.
- MIG is the first choice if you want to weld materials such as aluminum, magnesium, copper or titanium together.
How exactly does MIG/MAG welding work?
The MIG/MAG welding process begins with the ignition of the arc, which is initiated either by the welding wire itself or by a filler material. The constant voltage of the welding machine generates the electric plasma arc between the welding wire and the workpiece.
The pieces of metal are melted and join together accordingly. The melting welding rod serves both as an electrode and as a material feed, which makes the welding process faster than TIG welding.
Gas-filled welding rods are an option for TIG/MAG welding without a gas cylinder.
Which materials can be welded using the MIG/MAG process?
The short answer is: almost all of them! The methodology is indeed very flexible when it comes to selecting materials. You can use MIG/MAG welding technology to weld a wide range of materials such as aluminum, steel or stainless steel. Do you want to weld two different materials together? That’s no problem at all with this welding process. When MIG/MAG welding aluminum, you should only make sure to use the pulse function to protect the sensitive surface layer.
Get a quote for your parts
What are the advantages of MIG/MAG welding compared to other methods?
One of the biggest advantages of MIG/MAG welding compared to TIG welding, for example, is definitely its speed. The process can reduce welding times.
This works best when the process is automated, which speeds up the joining and thus the overall process. This makes the process very economical, especially for series production.
Another advantage of MIG/MAG welding is that, unlike other welding processes, it is relatively easy to learn. TIG welding is a lot trickier and requires more know-how and experience on the part of the welder.
Other positive features of the process are the short post-processing time and the wide variety of materials available. Additional material is usually inexpensive and distortion is generally very low.
All the advantages of MIG/MAG welding at a glance
- Short welding times, fast
- Economical
- Easy to learn
- Minimal post-processing time
- Low delay
- Large selection of materials
- Notably good properties in relation to thin sheet metal
- Also ideal for automated welding
One disadvantage is that the process is not suitable for applications that later come into contact with food, as it is not possible to ensure sterility. The workpiece may be more susceptible to rust than with other processes. Beautiful seams are possible under certain settings, but TIG welding is preferable in terms of a flawless appearance.
What should I pay particular attention to when MIG/MAG welding?
Accidents at work during welding can have unfortunate outcomes. It is therefore essential to take precautionary measures. Pay particular attention to these points when MIG/MAG welding:
- The MIG/MAG welding process is characterized by a particularly high level of radiation. The purchase of high-quality protective glasses with a high protection level is strongly recommended.
- The use of inert gases at high temperatures also means the release of potentially harmful combustion vapors. With respiratory protection, you are always on the safe side.
- MIG/MAG welding involves high voltage due to the use of electric current. Therefore, always observe all the necessary safety precautions that this entails.
Conclusion – MIG/MAG welding: economical and easy to learn
MIG/MAG welding is not so popular for nothing: short welding times make it economical and easy to learn. The MIG and MAG processes are combined in the name, as only the shielding gas changes during handling. The MAG process uses active gases, while the TIG process uses inert gases. MIG/MAG welding is the best choice for anyone who does not require perfect weld seams and is looking for a fast process, particularly for large quantities, which can also be automated.
Would you like to outsource the production of your components? Nothing could be easier!
As a professional digital manufacturer 4.0, we offer all innovative CNC production processes. Excellent customer service is a matter of course for us, which is why we also offer various special services, such as the production of complex precision components. Do you need your delivery yesterday? Unfortunately this is not possible, but express production within 72 hours is certainly feasible for us.
Does that sound good? Then get in touch with us today. We will send you an offer tailored to your project within 48 hours.
Optimization of your supplier search
Download Whitepaper
Find out now which 9 points you should consider so that you can find the right supplier and reduce your costs by up to 40%.
Please note that the whitepaper is only available in the German language.
